Improper Application Techniques: Common Errors That Compromise Protection
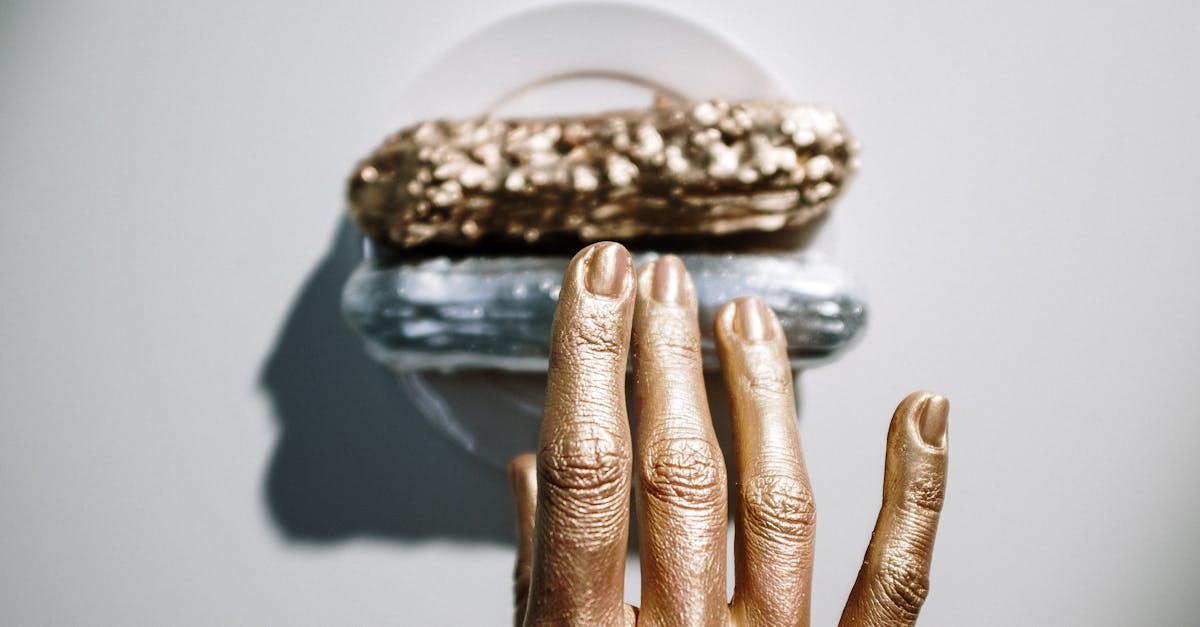
Table Of Contents
Equipment Misuse
The effectiveness of protective applications heavily relies on the correct use of equipment. Many users underestimate the importance of following the manufacturer's instructions and proper operational practices. Misconfigured or uncalibrated tools can lead to uneven distribution of the product. This inconsistency not only compromises protection but also results in wasted materials and increased costs.
Furthermore, using inappropriate equipment for specific tasks can lead to significant challenges. For instance, a sprayer that is ill-suited for the viscosity of the protective product may cause clogging or excessive overspray. Such inadequacies can ultimately result in a failure to achieve the desired level of protection. Proper selection and maintenance of equipment are critical in ensuring that applications are both effective and efficient.
Understanding the Importance of Proper Tools
Using the right tools is essential for achieving the desired results in any protective application. The tools you select can directly influence the uniformity of the application and the effectiveness of the protection being provided. For instance, using a high-quality sprayer can help deliver a consistent coat, reducing the risk of gaps or overlaps that may leave surfaces vulnerable. Furthermore, well-maintained equipment ensures that the materials are applied at the correct pressure and volume, which is crucial to ensuring the longevity of the protective layer.
Different tasks require specific tools tailored to the materials being worked with. For example, the choice between brushes, rollers, or sprayers depends on the surface type, the viscosity of the product, and the desired finish. An appropriate tool not only improves efficiency but also maximises the benefits of the protective products used. By prioritising the selection of proper tools, individuals can better safeguard their projects and achieve superior outcomes.
Lack of Preparation Before Application
Before applying any product, thorough preparation is crucial to ensuring effective results. Proper planning should include assessing the environmental conditions and the area of application. Weather conditions such as wind, rain, or extreme temperatures can affect the adhesion and lifespan of the product being applied. Moreover, having a clear understanding of the desired outcome helps in selecting the right techniques and materials needed for the task.
Additionally, neglecting to prepare the work area can lead to suboptimal application. Organising the space can prevent contamination from dust, dirt, or moisture, all of which can hinder the effectiveness of the product. Identifying potential obstacles and ensuring that all equipment and materials are easily accessible further contribute to a smooth application process. Taking the time to prepare properly not only enhances the quality of the application but also increases the overall efficiency of the job.
Necessary Steps to Ensure Optimal Results
Preparation plays a critical role in achieving the desired outcomes in any application process. Different types of materials may require specific steps to ensure compatibility. Identifying the right conditions for application is vital. Factors such as temperature, humidity, and even time of day can influence the performance of the product. Understanding these elements allows for better control over the application process and ensures that the product adheres to surfaces as intended.
Following manufacturer guidelines contributes significantly to optimal results. Each product often comes with detailed instructions regarding the amount to use, the ideal method of application, and the specific drying times. Adhering strictly to these recommendations reduces the risk of failures and enhances overall effectiveness. It is also useful to gather feedback from previous applications to identify any recurring issues and adjust techniques accordingly.
Inadequate Surface Preparation
Surface preparation plays a critical role in ensuring the effectiveness of any protective coating or treatment. When surfaces are not adequately cleaned or primed, contaminants such as dust, grease, or moisture can interfere with the adhesion of the product. As a result, the protective layer may fail to bond properly, leading to premature wear, peeling, or even complete failure of the application. This issue often goes unnoticed until significant damage has already occurred, causing costly repairs and maintenance.
Failure to assess the suitability of surfaces can also lead to compromised outcomes. Different materials, such as metals, wood, or concrete, require specific preparations to maximise the benefits of protective coatings. For instance, untreated wood may absorb moisture differently compared to treated surfaces, resulting in inconsistent application performance. Neglecting these important details not only diminishes the protective qualities of the product but can also lead to dissatisfaction with the results, prompting the need for reapplication or alternative solutions.
The Significance of Clean and Suitable Surfaces
Clean and suitable surfaces are crucial for effective application, as contaminants can undermine the effectiveness of the product. Dust, grease, or moisture may create barriers that prevent optimal adhesion, leading to subpar results. Additionally, certain surfaces may require specific treatments to ensure compatibility with the protective materials being applied. Ensuring that surfaces are prepped and primed can significantly enhance the longevity and overall performance of protective coatings.
Proper surface preparation not only improves adhesion but also contributes to a uniform finish. Any irregularities or blemishes on a surface can affect how the product spreads and settles. Achieving a smooth base allows for an even application, which is essential when aiming for maximum protection. Surface cleanliness and suitability, therefore, serve as foundational steps in the application process that cannot be overlooked.
FAQS
What are some common equipment misuse errors when applying protective products?
Common equipment misuse errors include using the wrong type of applicator, failing to calibrate spray equipment correctly, and neglecting to clean tools after previous uses, which can lead to contamination and ineffective application.
Why is it important to use proper tools during application?
Using proper tools is crucial because they are designed to deliver the product evenly and effectively. Incorrect tools can lead to uneven coverage, wasted materials, and ultimately, compromised protection.
What preparation steps should be taken before applying protective coatings?
Preparation steps include reading the product label for specific instructions, ensuring the work area is clear and accessible, and checking weather conditions. It's also important to gather all necessary tools and protective gear before starting the application.
How does inadequate surface preparation affect the application process?
Inadequate surface preparation can lead to poor adhesion, uneven application, and even product failure. Surfaces must be clean, dry, and suitable for the product being applied to ensure optimal results.
What are the key factors to ensure surfaces are properly prepared for application?
Key factors include cleaning the surface to remove any dirt, grease, or contaminants, repairing any damage, and ensuring the surface is dry and appropriately primed if necessary. This ensures that the protective product adheres correctly and performs effectively.
Related Links
Neglecting to Rinse Thoroughly: The Dangers of Leaving Residue on Coated SurfacesSkipping Regular Inspections: The Importance of Monitoring Your Coating's Condition
Inadequate Surface Preparation: The Essential First Step Not to Overlook
Using Automatic Car Washes: Why Hand Washing is Safer for Coated Vehicles
Failing to Follow Manufacturer Guidelines: Understanding the Importance of Instructions
Applying Wax Over Ceramic Coatings: A Mistake You Don’t Want to Make