The Impact of Surface Temperature on Coating Adhesion
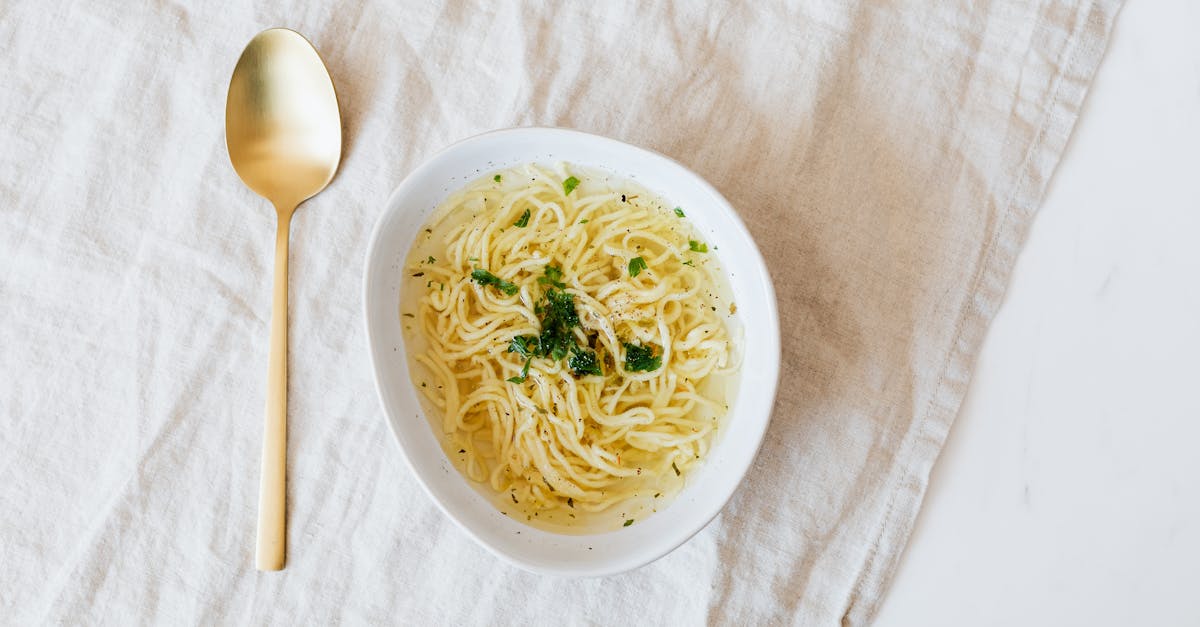
Table Of Contents
Effects of High Surface Temperatures
High surface temperatures can significantly influence coating adhesion, often leading to challenges in achieving optimal performance. When surfaces are heated beyond recommended levels, the risk of thermal degradation increases. This can lead to a breakdown of the coating materials, altering their chemical composition and potentially resulting in delamination or poor bonding. Furthermore, the elevated temperatures may cause uneven application, which can create weak spots in the coating that compromise its durability.
The effects of high temperatures are not merely isolated to the immediate application environment. They can lead to extended curing times and the possibility of hazardous off-gassing from certain substances used in coatings. Applicators need to be keenly aware of these risks and take proactive measures to mitigate them. Using temperature monitoring devices can help ensure that surface temperatures remain within recommended ranges during the application process, promoting better adhesion and overall performance of the coating.
Challenges and Solutions in Coating Performance
High surface temperatures can pose significant challenges for coating performance, particularly through issues related to rapid drying times and the risk of reduced adhesion. Coatings applied in hot conditions may cure too quickly, preventing proper bonding with the substrate. Additionally, thermal expansion can alter the substrate's properties, leading to cracks or delamination of the coating. Ensuring uniform coverage can also become more difficult, increasing the likelihood of weak spots within the coating.
To address these challenges, adjusting application techniques and materials is essential. One effective strategy involves selecting coatings designed for higher temperature ranges, which maintain flexibility and adhesion under adverse conditions. Implementing controlled application processes can help manage the temperature during the coating process. Adequate surface preparation, like cleaning and priming, also plays a crucial role in enhancing adhesion, resulting in improved long-term performance of the coating in fluctuating temperatures.
Effects of Low Surface Temperatures
Low surface temperatures can significantly hinder the adhesion of coatings to various substrates. When temperatures drop, the viscosity of coating materials often increases, making them more challenging to apply evenly. This change in viscosity can lead to a poor bond between the coating and the substrate, resulting in uneven coverage and potential defects. Furthermore, low temperatures can slow down the curing and drying processes, increasing the likelihood of defects such as bubbling or cracking.
Another concern with low surface temperatures is the potential for moisture accumulation. Condensation can form on cold surfaces, which may result in a film of moisture that interferes with adhesion. If coatings are applied under these conditions, they may not cure correctly or may lift after application. To ensure optimal adhesion, it is crucial to monitor environmental conditions and implement strategies such as preheating surfaces or using temperature-controlled application environments, which can promote better coating performance.
Risks and Mitigation Strategies for Adhesion
Surface temperatures that dip too low can lead to numerous challenges in coating adhesion. One significant risk involves the inability of the coating material to properly wet and bond to the substrate. When surfaces are cold, any moisture present can condense, creating a barrier that prevents effective adhesion. Additionally, low temperatures can alter the viscosity of the coating, resulting in improper application and coverage.
To mitigate these risks, it is crucial to carry out thorough surface preparation and temperature management. Preheating the substrate can enhance the adhesion properties by creating an optimal surface condition. Heating blankets or heat guns may be employed to achieve the desired temperature before coating application. Furthermore, selecting coatings designed for colder environments can ensure better performance and adhesion, even under less than ideal conditions.
Preparing Surfaces for Coating
Effective surface preparation is crucial for ensuring optimal coating adhesion. This process often involves cleaning the surface to eliminate contaminants such as dust, grease, or previous coatings. Utilising appropriate solvent or detergent can drastically improve the quality of adhesion. Surface roughness also plays a vital role. Techniques like sanding, blasting, or using a wire brush can enhance the mechanical interlock between the coating and the substrate.
Temperature management should not be overlooked during the preparation phase. Surfaces exposed to extreme temperatures can affect both the cleaning process and the application of coatings. Timing is essential; coatings should be applied when the temperature is within the recommended range for best adhesion outcomes. Conducting thorough inspections post-cleaning and ensuring a controlled environment can greatly improve coating performance, reducing the likelihood of premature failure.
Best Practices for Temperature Management
Managing surface temperature effectively is crucial for achieving optimal coating adhesion. Begin by monitoring environmental conditions carefully. Using infrared thermometers or thermal imaging can help assess temperatures accurately prior to application. If surface temperatures are too high, implement shade mechanisms to cool surfaces or schedule applications during cooler times of the day. Conversely, if temperatures are low, consider using heaters or heat lamps to bring surfaces up to the desired range, ensuring that these methods do not alter the integrity of the substrate.
Preparation techniques significantly influence the success of temperature management in coating processes. Ensure that surfaces are cleaned of contaminants that may hold heat or cold unevenly. Engaging in appropriate surface preparation methods, such as blast cleaning or sanding, can promote better adhesion and minimise temperature discrepancies. Additionally, adjusting the coating formulation to accommodate specific temperature ranges can enhance performance. Implementing these strategies will help maintain ideal conditions throughout the coating application process.
FAQS
How does high surface temperature affect coating adhesion?
High surface temperatures can lead to issues such as inadequate curing, thermal expansion mismatches, and premature drying of the coating, all of which can compromise adhesion.
What challenges are commonly faced with coating performance under high temperatures?
Challenges include blistering, bubbling, and peeling of the coating, as well as altered drying times and potential degradation of the coating materials.
What are the risks associated with low surface temperatures when applying coatings?
Low surface temperatures can cause poor adhesion, increased viscosity of the coating materials, and extended drying times, which may lead to incomplete bonding or defects.
How can surface preparation improve coating adhesion in varying temperatures?
Proper surface preparation, such as cleaning, sanding, and priming, ensures better adhesion by providing a suitable substrate that enhances the bonding between the surface and the coating, regardless of temperature.
What best practices should be followed for temperature management during coating application?
Best practices include monitoring environmental conditions, adjusting application techniques based on temperature, using temperature-appropriate coatings, and ensuring adequate heating or cooling of surfaces as needed.
Related Links
Steps to Achieve Optimal Paint DecontaminationImportance of Thorough Surface Cleaning Before Application
Benefits of Clay Bar Treatment in Preparation
Preparing Glass and Trim for Ceramic Coating
Understanding the Role of Paint Correction in Application