The Importance of Quality Polishing Pads in Ceramic Coating
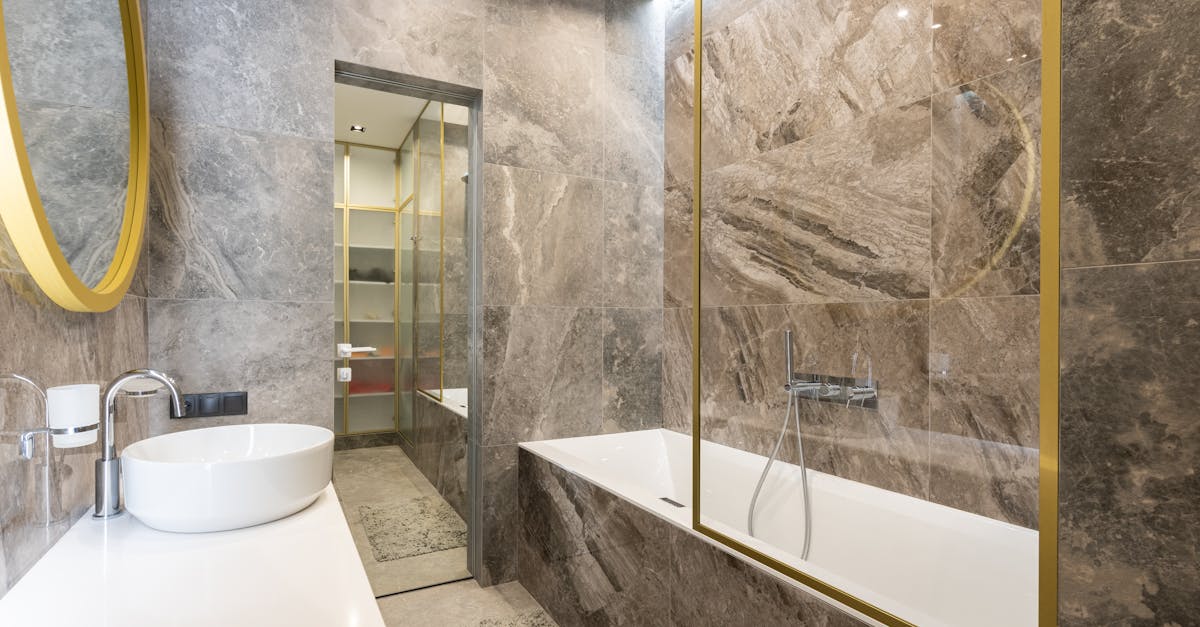
Table Of Contents
Techniques for Using Polishing Pads Effectively
Using polishing pads requires a thoughtful approach to achieve optimal results. It's essential to choose the right pad for the specific task at hand, considering both the type of surface and the kind of finish desired. Different pads vary in their density and material, impacting the polishing action. For instance, softer pads are suitable for applying a ceramic coating, while denser options may be more appropriate for initial surface correction. Adjusting the machine speed according to the task can also influence the effectiveness, ensuring the pad operates at an optimal level for the application.
Technique plays a critical role in the application process. It is important to work in small, manageable sections to maintain a consistent finish. Overlapping passes can help avoid streaks and uneven coverage. Applying even pressure across the entire pad enhances the distribution of the product. Maintaining a steady motion prevents the risk of burning or damaging the surface. Regular checking in between sections helps to ensure that the coating is being applied uniformly without any skips or inconsistencies.
Best Practices for Optimal Results
To achieve the best outcomes, it is essential to select the right type of polishing pad for the specific ceramic coating being used. Different pads offer varying levels of cut and finish, influencing the overall appearance and durability of the coating. Using a pad that complements the coating can enhance the application process, allowing for a smoother finish while preventing damage to the surface underneath. Regularly assessing the condition of the pad throughout the job will ensure the quality of application remains high.
Utilising an appropriate polishing technique also plays a significant role in achieving optimal results. Applying even pressure while moving the pad in a consistent pattern helps to distribute the product evenly across the surface. Taking care not to overheat the pad or the coating will preserve their integrity, leading to a more durable finish. Working in a controlled environment with suitable temperature and humidity levels can further improve the performance of the ceramic coating application, contributing to long-lasting results.
Maintaining Your Polishing Pads
Regular maintenance of polishing pads greatly extends their lifespan and effectiveness. After each use, it’s essential to remove any residue and contaminants. A gentle tap or a brush specifically designed for pads can help dislodge particles. For deeper cleaning, a solution of warm water and a mild detergent works wonders. Soaking the pads briefly and then rinsing them thoroughly ensures that no cleaning agents remain, which could interfere with future applications.
Proper storage is equally important to maintain the integrity of the polishing pads. Keep them in a cool, dry place away from direct sunlight to prevent any deformation caused by heat. Stacking pads neatly, either on a shelf or in a dedicated storage container, helps avoid unnecessary compression. Ensure that the pads are completely dry before storing them to prevent mould or mildew growth, which can adversely affect their performance when it's time to polish again.
Cleaning and Storing for Longevity
Proper maintenance of polishing pads significantly impacts their performance and lifespan. After each use, it is crucial to remove any residues of polish, dust, or debris that may have accumulated. Gentle cleaning with warm water and a mild detergent is often effective in ensuring that no product remains trapped within the fibres. Rinsing them thoroughly and allowing them to air dry in a well-ventilated area helps avoid mould and mildew growth, which can compromise the pad’s efficacy.
Storing polishing pads correctly prolongs their usability and maintains their structure. They should be kept in a cool, dry place away from direct sunlight to prevent any degradation of the materials. Avoid stacking them directly on top of each other; instead, use dividers or a dedicated storage container to preserve their shape. Taking these simple precautions ensures that your polishing pads remain in optimal condition, ready for your next ceramic coating project.
Common Mistakes to Avoid
One frequent oversight is using the wrong pad for the specific task at hand. Each polishing pad is designed with unique characteristics suitable for various surfaces and finishes. Selecting a pad that is too abrasive can lead to micro-marring, damaging the ceramic coating. Equally, employing a pad that is too soft may fail to achieve the desired level of gloss. Understanding the purpose and suitability of each pad can significantly influence the final outcome.
Another common error involves neglecting the proper speed and pressure when using the tools. It is vital to adhere to recommended settings for both the machine and the pad to avoid overheating and excessive wear. Applying too much pressure may not expedite the process but rather lead to uneven results. Regularly varying the pressure throughout the polishing procedure allows for a more controlled application, ensuring an even finish.
Errors That Can Compromise the Coating
Improper application techniques can significantly diminish the effectiveness of ceramic coatings. Common errors include applying too much pressure while buffing, which can create swirl marks or damage the delicate surface. Additionally, using a dirty or inappropriate polishing pad can introduce contaminants, leading to an uneven finish. These mistakes not only affect the aesthetic qualities of the coating but can also compromise its durability and protective properties.
Overlooking environmental factors during the application process is another aspect that can undermine a ceramic coating's performance. High temperatures and direct sunlight can cause the product to cure too quickly, resulting in improper bonding to the surface. Similarly, applying the coating in a humid environment may lead to moisture being trapped beneath the layer, which can ultimately promote peeling or discolouration. Paying attention to the conditions during application is essential to ensure a long-lasting and high-quality finish.
FAQS
Why are quality polishing pads important for ceramic coating?
Quality polishing pads are crucial for achieving an even and durable ceramic coating finish. They help to effectively remove imperfections from the surface, ensuring better adhesion of the coating and enhancing the overall appearance of the vehicle.
What are some techniques for using polishing pads effectively?
Effective techniques include using the correct pad for the specific surface type, maintaining a consistent speed and pressure while polishing, and working in small sections to ensure thorough coverage and optimal results.
How can I maintain my polishing pads for longevity?
To maintain polishing pads, it's important to clean them after each use to remove residue and contaminants. Store them in a cool, dry place away from direct sunlight, and avoid stacking them to prevent deformation.
What are common mistakes to avoid when using polishing pads?
Common mistakes include using the wrong type of pad for the coating, applying too much pressure, and neglecting to clean the pads regularly. These errors can compromise the quality of the ceramic coating and lead to subpar results.
How often should I replace my polishing pads?
The frequency of replacing polishing pads depends on usage and wear. Generally, if you notice a decrease in performance, visible wear and tear, or if the pads become hard or discoloured, it may be time to replace them for optimal results.
Related Links
Comparing Different Applicators for Ceramic CoatingProfessional-Grade Tools for Achieving a Flawless Ceramic Finish
Essential Paint Correction Tools Before Applying Ceramic Coatings
Top Detailing Brushes for Ceramic Coating Applications
Choosing the Right Surface Prep Products for Ceramic Coating
Recommended Pressure Washers for Pre-Cleaning Surfaces
Must-Use Safety Gear for Ceramic Coating Applications
Must-Have Equipment for DIY Ceramic Coating Projects
Essential Tools for a Successful Ceramic Coating Application