The Science Behind UV Resistance in Ceramic Coatings
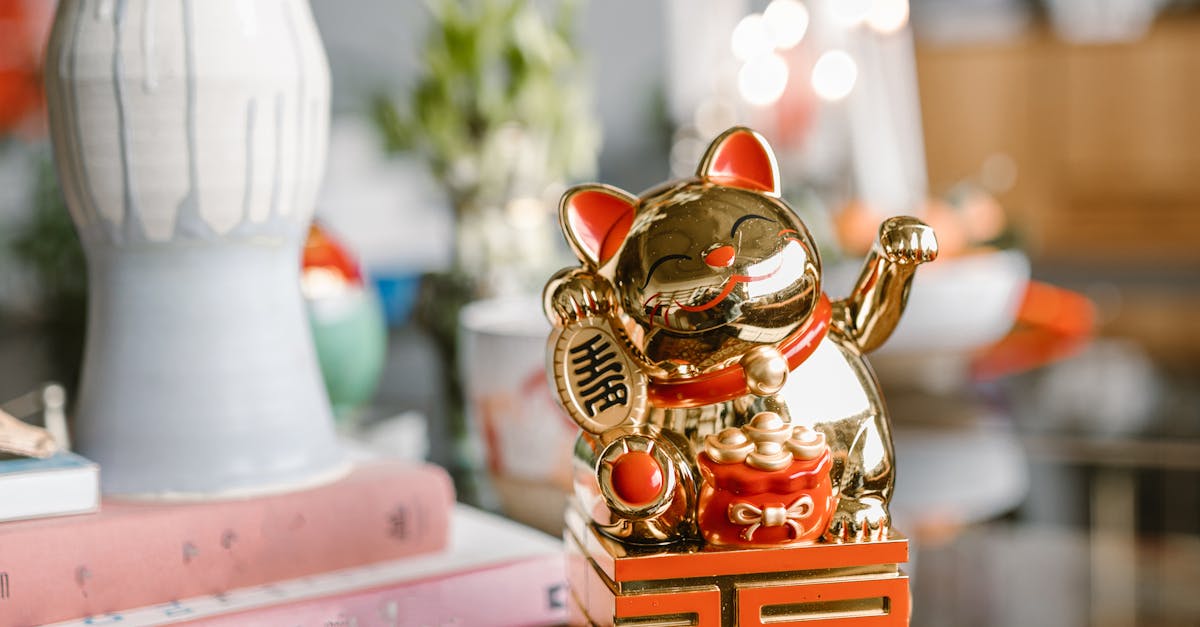
Table Of Contents
Applications of UV Resistant Ceramic Coatings
UV resistant ceramic coatings are employed across various sectors, owing to their durability and protective qualities. Automotive applications frequently utilise these coatings to protect paintwork from sun damage and fading. Not only do they enhance aesthetic appeal, but they also prolong the life of vehicles by providing a robust shield against harmful ultraviolet rays.
Another significant application lies within architectural and industrial sectors. Buildings featuring UV resistant ceramic coatings benefit from reduced wear and tear on exterior surfaces, leading to lower maintenance costs. In the manufacturing field, these coatings are used on machinery and tools, preventing degradation from prolonged exposure to sunlight, thereby enhancing their operational lifespan.
Industries that Benefit from UV Protection
Numerous industries leverage UV-resistant ceramic coatings to enhance the durability and aesthetics of their products. Automotive manufacturers frequently use these coatings to protect vehicle finishes from sun damage, preserving the paint's vibrancy and integrity over time. In construction, UV-resistant ceramics safeguard building materials and surfaces against the harsh Australian sun, extending the lifespan of roofs and facades while minimising maintenance costs.
The aerospace industry also benefits significantly from UV protection, as aircraft surfaces require coatings that withstand intense UV exposure at high altitudes. This ensures both performance and safety. Additionally, outdoor furniture manufacturers utilise these coatings to maintain the appearance and functionality of their products against environmental factors, increasing customer satisfaction and encouraging eco-friendly practices in design and manufacturing.
Testing UV Resistance in Ceramic Coatings
Assessing the UV resistance of ceramic coatings involves a variety of standardized testing methods. These methods are designed to simulate real-world exposure to UV radiation and measure the degradation or changes in the properties of the coatings over time. Common techniques include accelerated weathering tests, where samples are subjected to intense light and heat in controlled environments. Such tests provide valuable data on durability and longevity, essential for applications facing harsh sunlight.
Evaluations often focus on parameters such as colour stability, adhesion strength, and surface integrity. By quantitatively analysing these attributes, manufacturers can compare the performance of different ceramic coatings. This process ensures that only coatings meeting stringent UV resistance standards are brought to market, reinforcing their suitability for applications in industries ranging from automotive to architecture.
Standardized Methods and Evaluations
Numerous standardized methods have been established to evaluate the UV resistance of ceramic coatings. These methods often involve exposure to artificial UV light sources that simulate sunlight. The tests typically measure the performance of coatings over specified timeframes, assessing factors such as gloss retention, colour stability, and mechanical properties. Standard protocols, such as ASTM G154 and ISO 4892, provide consistent procedures for ensuring that results are reliable and comparable across different products and manufacturers.
Evaluations often include accelerated weathering tests, which subject coatings to various environmental conditions, including humidity, temperature fluctuations, and UV radiation. This approach highlights a coating's performance in real-world scenarios. Results from these tests help manufacturers refine their formulations and ensure that they meet industry standards. By utilising these established testing methods, stakeholders can make informed decisions regarding the suitability of ceramic coatings for specific applications.
Comparing UV Resistance in Different Coating Types
Different coating types exhibit varying levels of UV resistance, which directly impacts their longevity and performance. Ceramic coatings stand out due to their ability to withstand intense UV radiation without degrading. This durability is attributed to their unique molecular structure, which absorbs and dissipates energy more efficiently than traditional coatings. In contrast, many conventional coatings, such as paints or varnishes, often rely on organic compounds that can break down under UV exposure, leading to fading, chalking, and peeling.
When comparing ceramic coatings to their traditional counterparts, the differences in longevity and maintenance become evident. Traditional coatings may require more frequent reapplication or maintenance due to their susceptibility to UV damage. In contrast, ceramic coatings not only enhance aesthetic appeal but also offer significant protection against environmental stressors, including UV rays. This makes ceramic coatings a more cost-effective and practical choice for applications where long-term performance is critical.
Ceramic vs. Traditional Coating Solutions
Ceramic coatings have gained considerable attention due to their superior UV resistance when compared to traditional coating solutions. These coatings utilise inorganic compounds that form a hard, protective layer, effectively shielding surfaces from harmful UV rays. The durability of ceramic coatings enhances their lifespan, making them a favourable option for applications requiring long-lasting protection. Traditional coatings often rely on organic compounds and polymers, which can degrade more quickly under prolonged exposure to sunlight, leading to discoloration, chalking, and reduced performance.
Moreover, ceramic coatings typically exhibit better adhesion properties and resistance to environmental contaminants. This characteristic not only extends the life of the surface they're applied to but also reduces the frequency and costs associated with reapplication. Traditional coatings may require more frequent maintenance, which can be burdensome for industries that prioritise efficiency. The distinct properties of ceramic coatings position them as a preferred choice for both residential and commercial applications seeking long-term UV protection.
FAQS
What are UV resistant ceramic coatings?
UV resistant ceramic coatings are protective layers applied to surfaces to shield them from harmful ultraviolet (UV) rays, significantly reducing degradation and maintaining the integrity of materials over time.
How do ceramic coatings compare to traditional coatings in terms of UV resistance?
Ceramic coatings typically offer superior UV resistance compared to traditional coatings, as they are designed to bond more effectively and provide longer-lasting protection against UV-induced damage.
What industries benefit from using UV resistant ceramic coatings?
Industries such as automotive, aerospace, marine, and construction benefit from UV resistant ceramic coatings due to their ability to enhance durability and prolong the life of materials exposed to sunlight.
How is the UV resistance of ceramic coatings tested?
The UV resistance of ceramic coatings is tested using standardized methods that evaluate their performance under simulated UV exposure, assessing factors such as colour stability, gloss retention, and overall degradation.
Are there specific standards for testing UV resistance in coatings?
Yes, there are standardized methods and evaluations established by organisations such as ASTM (American Society for Testing and Materials) and ISO (International Organization for Standardization) that provide guidelines for assessing UV resistance in coatings.
Related Links
Preventing Paint Fade: The Role of Ceramic CoatingHow Ceramic Coating Shields Your Vehicle from Harmful UV Rays
The Benefits of Ceramic Coating in Harsh Australian Sun Conditions
Understanding the UV Protection Properties of Quality Ceramic Coatings
Why UV Protection is Essential for Vehicle Maintenance
The Impact of UV Damage on Vehicle Appearance