Timing Your Maintenance: Frequency Factors for Different Conditions
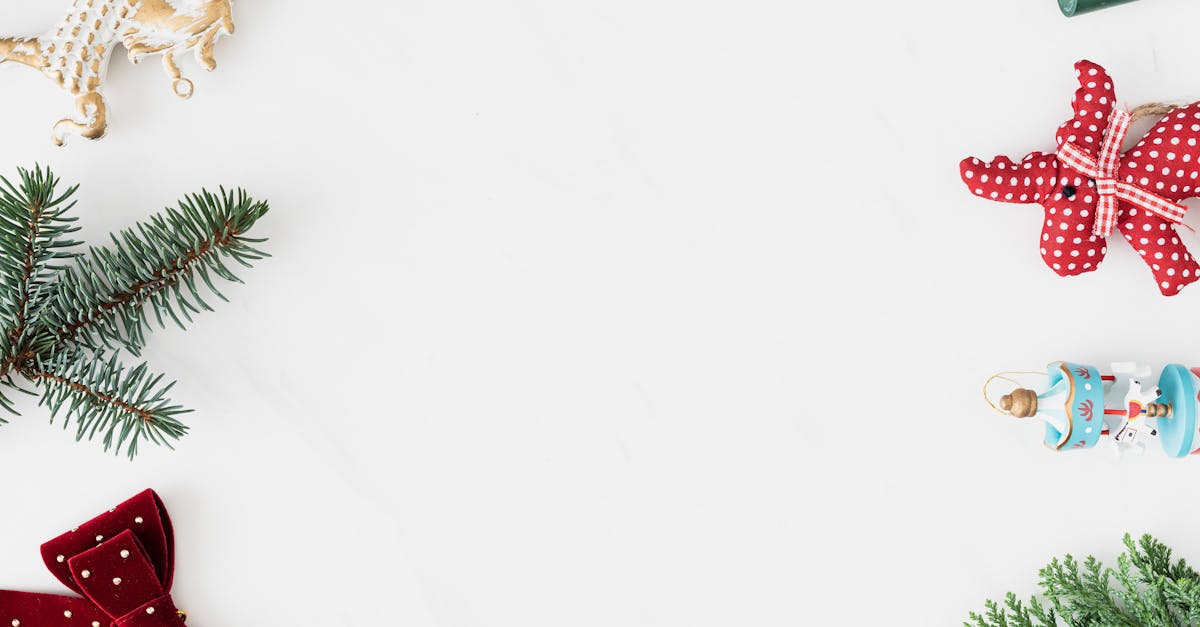
Table Of Contents
Specific Industry Requirements
Different industries have distinct maintenance requirements driven by operational demands, safety regulations, and equipment complexity. In sectors like manufacturing, regular machinery upkeep is critical to ensure optimal performance and prevent costly downtime. Companies often adhere to strict maintenance schedules dictated by the machinery manufacturers, which can vary based on the type of equipment and its intended use. Additionally, larger operations may implement predictive maintenance techniques that leverage data analytics to anticipate potential failures and address them before they impact production.
In contrast, industries such as healthcare prioritise compliance with stringent regulatory standards. Equipment in this sector must undergo more frequent inspections and servicing to meet safety protocols and ensure patient wellbeing. This leads to structured maintenance routines that not only address functionality but also uphold legal obligations. In summary, the nature of an industry significantly shapes its maintenance needs, influencing how often and in what manner these tasks are executed.
Unique Needs in Different Sectors
Different industries have distinct operational needs that influence their maintenance strategies. For example, the healthcare sector requires stringent protocols for equipment maintenance, as any downtime can directly impact patient care. Regular servicing must ensure that medical devices operate at peak performance while also adhering to safety standards. Similarly, the aviation industry places a high premium on maintenance schedules, as compliance with safety regulations is critical for both equipment longevity and passenger safety.
In the manufacturing sector, machinery maintenance is deeply tied to production efficiency. Downtime due to maintenance can lead to significant financial losses, prompting many manufacturers to adopt predictive maintenance strategies. These strategies utilise data analytics and technology to anticipate failures before they occur, allowing for more streamlined operations. On the other hand, facilities in the hospitality industry may focus more on aesthetic upkeep and functionality to enhance guest experiences, requiring a different approach to maintenance that emphasises rapid response and attention to detail.
Local Regulations and Standards
Local regulations often dictate the maintenance schedule for various industries. Adhering to these guidelines is crucial for ensuring safety and compliance. Industries such as construction, healthcare, and food service face strict regulatory scrutiny. Regular inspections and maintenance routines help organisations avoid fines and penalties, ensuring they operate within established legal frameworks.
Meeting local standards not only protects public safety but also enhances a company’s reputation. Non-compliance can lead to legal repercussions and increased liability. Businesses must stay updated with any changes in regulations to adequately adjust their maintenance practices. This proactive approach helps in mitigating risks associated with outdated procedures and equipment.
Compliance with Regional Guidelines
Navigating the complexities of local regulations is essential for businesses operating in various sectors. Each region may enforce specific guidelines that dictate the frequency and nature of maintenance activities. Compliance not only ensures the safety and longevity of equipment but also protects organisations from potential fines and legal ramifications. Understanding these requirements is crucial for aligning maintenance schedules with legal obligations.
Moreover, adhering to regional standards can enhance a company’s reputation and credibility in the market. Many clients prefer engaging organisations that demonstrate due diligence in meeting compliance protocols. Regular audits and updates to maintenance practices can help businesses stay in line with evolving regulations. This proactive approach minimises disruptions and reinforces a commitment to quality and safety in operations.
Financial Considerations
Budgeting for maintenance costs requires an understanding of both the immediate and long-term financial implications. Regular maintenance can prevent larger, unexpected expenses that often arise from neglected equipment or facilities. Establishing a clear maintenance schedule helps allocate funds more efficiently, ensuring that resources are available when needed.
In addition to direct costs, businesses must also consider potential disruptions to operations during maintenance periods. Downtime can lead to lost revenue and affect productivity. It is vital to strike a balance between regular upkeep and the financial strain of halting operations for repairs. Factors such as the age of equipment and usage intensity should be considered when formulating a budget for ongoing maintenance.
Budgeting for Maintenance Costs
Evaluating maintenance costs is essential for both short-term and long-term budgeting. Regular assessments of equipment and facility needs help identify areas where expenses can be reduced. Planning for unexpected repairs is equally important, ensuring that funds are allocated to mitigate disruptions to operations. A proactive approach can lead to better resource allocation and more efficient use of the budget.
Integrating maintenance costs into overall financial planning requires a thorough understanding of industry standards and specific operational needs. Prioritising maintenance tasks based on urgency and importance can help manage expenses effectively. By developing a clear framework for these costs, organisations can enhance their financial sustainability. This practice allows for informed decision-making that aligns with both operational goals and available financial resources.
FAQS
Why is it important to time maintenance correctly in different industries?
Timing maintenance correctly is crucial as it ensures optimal performance, compliance with regulations, and minimises downtime, ultimately contributing to overall efficiency and cost-effectiveness within various industries.
How do specific industry requirements affect maintenance frequency?
Different industries have unique operational demands, equipment types, and risk factors that dictate maintenance frequency. For instance, manufacturing may require more frequent checks compared to a less intensive sector like retail.
What role do local regulations play in determining maintenance schedules?
Local regulations often set minimum standards for maintenance frequency to ensure safety, environmental protection, and operational compliance. Adhering to these guidelines is essential to avoid penalties and maintain operational integrity.
How can businesses budget for maintenance costs effectively?
Businesses can budget for maintenance costs by assessing past maintenance expenses, evaluating the equipment's lifecycle, and anticipating future needs based on industry standards and regulatory requirements.
What are the consequences of neglecting timely maintenance?
Neglecting timely maintenance can lead to equipment failures, safety hazards, increased repair costs, and non-compliance with regulations, all of which can significantly impact a business's operations and profitability.
Related Links
Best Practices for Regularly Maintaining Ceramic CoatingsSigns That Indicate It's Time for Ceramic Coating Maintenance
How Seasonal Changes Affect Maintenance Frequency for Coated Surfaces
The Importance of Consistency in Ceramic Coating Upkeep
Monthly vs Quarterly Maintenance for Ceramic Coated Surfaces
Setting Up a Routine for Optimal Ceramic Coating Performance