Best Practices for Working with High-Pressure Application Tools
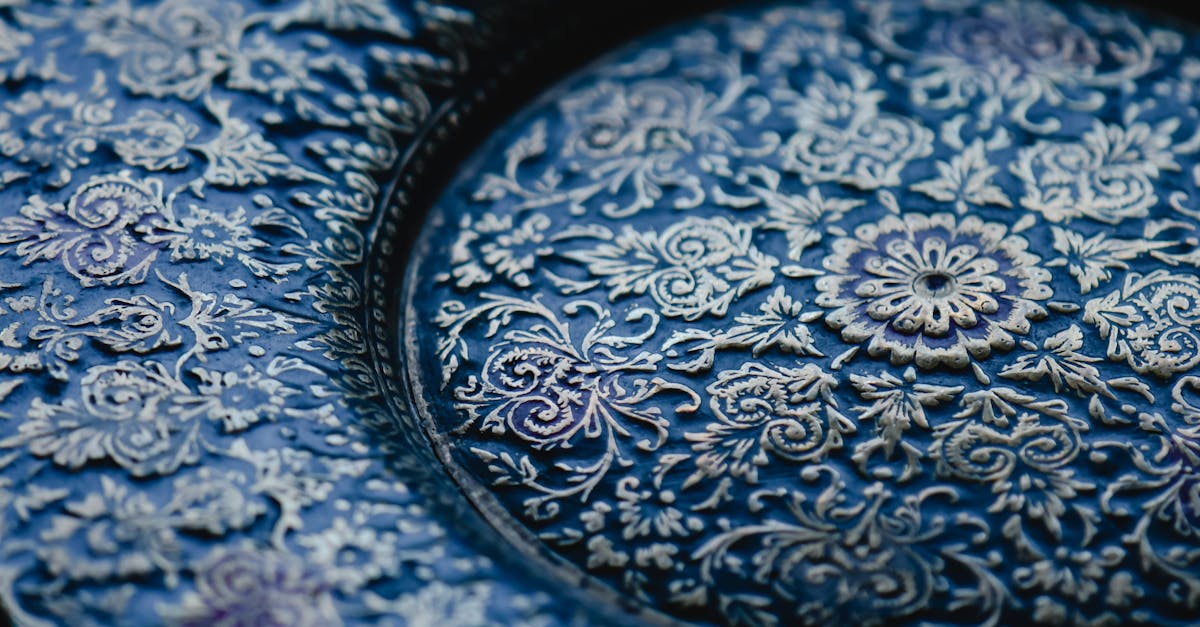
Table Of Contents
Troubleshooting Common High-Pressure Tool Issues
High-pressure tools can frequently present issues that may disrupt workflow. Common problems include leaks, irregular pressure readings, and unexpected shut-offs. Regular inspections can help identify potential malfunctions early. Operators should routinely check seals, hoses, and connections for wear and tear. It's also important to ensure that the equipment is correctly calibrated to avoid operational discrepancies.
When encountering performance problems, operators should systematically assess each component of the tool. Checking for clogs in filters or nozzles can often reveal underlying issues affecting efficiency. If the tool suddenly becomes unresponsive, reviewing the power supply and controls may uncover electrical faults. In some cases, consulting the manufacturer's manual can provide valuable insights into resolving specific issues effectively.
Identifying and Resolving Performance Problems
Performance problems with high-pressure application tools can often stem from improper maintenance or operator error. Regular inspections are crucial in identifying wear and tear on components such as hoses, fittings, and seals. A thorough understanding of the tool's operation manual helps operators recognise what normal performance looks like. Any deviation from this standard may signal an underlying issue that requires immediate attention.
In cases where performance issues arise, a systematic troubleshooting approach is advisable. Operators should first eliminate the most straightforward possibilities, such as inadequate power supply or blockages in hoses. Next, they can check for leaks, which can significantly impact pressure levels. If problems persist, consulting technical support or a service technician may provide additional insights into more complex issues that require specialised knowledge to resolve.
Training and Certification for High-Pressure Tool Use
Proper training and certification are vital components when it comes to safely operating high-pressure tools. These tools require specific skill sets to handle effectively. Operators must not only familiarise themselves with the equipment but also understand the associated risks. Comprehensive training programs typically cover operational procedures, maintenance checks, and safety protocols. This preparation helps ensure that operators can identify potential hazards before they escalate into serious issues.
Certification serves as a formal recognition of an operator's competency in managing high-pressure applications. It often involves practical assessments and theoretical examinations. By achieving certification, individuals demonstrate their ability to operate tools safely and efficiently. This process enhances workplace safety and instils confidence among team members and supervisors. Ultimately, investing in training and certification leads to reduced accidents and improved overall performance within high-pressure environments.
Importance of Skilled Operators in Ensuring Safety
The operation of high-pressure tools involves inherent risks that can have serious consequences if not managed properly. Skilled operators possess the necessary training and expertise to handle these tools safely. They understand the mechanics involved, which allows them to perform their tasks with confidence. This knowledge is critical in diagnosing potential safety hazards before a situation escalates.
Moreover, experienced operators contribute significantly to a safety culture within their workplaces. Their proficiency enables them to conduct regular maintenance checks and adhere to safety protocols. Through their actions, they set an example for less experienced colleagues. Establishing a team of competent users ensures a more vigilant approach to workplace safety, ultimately minimising accidents and injuries associated with high-pressure applications.
Environmental Considerations in High-Pressure Applications
High-pressure applications regularly raise concerns regarding their environmental impact. The discharge of wastewater containing chemicals and debris can lead to contamination of local ecosystems. Implementing proper waste management strategies and adhering to regulations becomes essential for minimising these risks. Additionally, using biodegradable or environmentally friendly cleaning agents can significantly lower harmful effects on surrounding flora and fauna.
Another factor to consider involves energy consumption in high-pressure operations. Energy-intensive tools not only increase operational costs but also contribute to greenhouse gas emissions. Opting for more efficient machinery and regularly maintaining existing equipment can help reduce energy usage. Furthermore, training operators on sustainable practices ensures that awareness of these environmental considerations remains a priority in daily operations.
Reducing Environmental Impact While Using These Tools
The effective use of high-pressure application tools can significantly contribute to minimising environmental impact. Selecting the right tools and techniques plays a crucial role in this endeavour. Using equipment designed for efficiency reduces resource consumption and lowers the carbon footprint associated with high-pressure methods. Regular maintenance of tools ensures optimal performance and prevents leaks or malfunctions that can lead to environmental damage.
Incorporating eco-friendly practices in operational procedures helps in further reducing impacts. Employing biodegradable or less harmful cleaning agents can minimise chemical runoff into the surrounding environment. Training operators to adopt waste minimisation techniques, such as effective water management and proper disposal of contaminants, enhances sustainability efforts. These strategies not only comply with regulations but also reflect a commitment to responsible environmental stewardship in the equipment industry.
FAQS
What are some common issues I might face when using high-pressure application tools?
Some common issues include leaks, inconsistent pressure, and overheating. Regular maintenance and proper troubleshooting can help identify and resolve these problems.
How can I improve the performance of my high-pressure tools?
Improving performance can be achieved by ensuring regular maintenance, using the correct attachments, and checking for any blockages in hoses or nozzles that might affect pressure.
Why is training important for operating high-pressure tools?
Training is crucial as it ensures that operators understand the proper handling and safety procedures, reducing the risk of accidents and improving overall efficiency in tool use.
What certifications should I look for when hiring someone to operate high-pressure tools?
Look for certifications that demonstrate proficiency in high-pressure tool operation, safety training, and any relevant industry-specific qualifications.
How can I minimise the environmental impact of using high-pressure tools?
You can reduce environmental impact by using eco-friendly cleaning solutions, ensuring proper disposal of waste, and regularly maintaining tools to prevent leaks and emissions.
Related Links
Fire Safety Measures When Using Ceramic CoatingsEssential Tips for Safe Mixing of Ceramic Coating Chemicals
Safety Guidelines for Handling Ceramic Coating Equipment
Importance of Skin Protection During Ceramic Coating Application
Recognising Allergic Reactions to Ceramic Coating Materials
First Aid Measures for Ceramic Coating Accidents