Fire Safety Measures When Using Ceramic Coatings
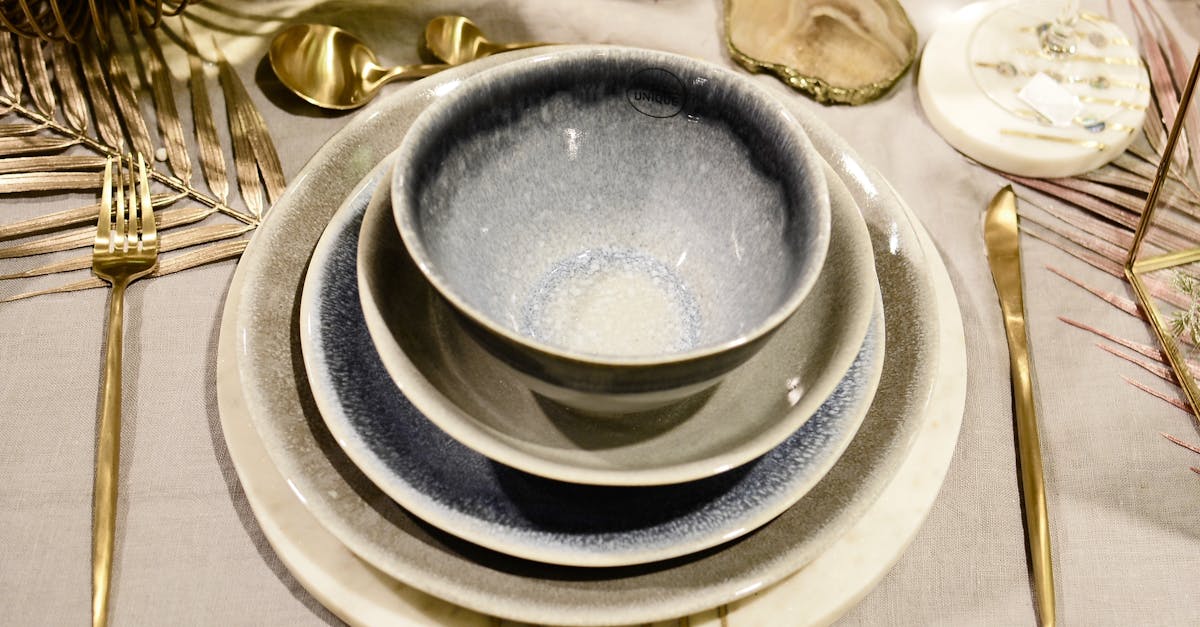
Table Of Contents
Curing and Drying Times
Properly understanding curing and drying times is essential for achieving the best results when working with ceramic coatings. These times can vary based on the specific product used, ambient conditions, and application techniques. Typically, the initial curing phase may take several hours, while complete curing can extend over days. Factors such as humidity and temperature can significantly influence these processes, making it critical to adhere to manufacturer guidelines.
Monitoring the conditions during curing can prevent issues like improper adhesion or finish imperfections. To ensure optimal results, it is advisable to avoid exposing freshly applied coatings to conditions that may interrupt the curing process. Adopting a systematic approach by scheduling applications according to weather forecasts can help in planning when to apply the coatings for a successful outcome.
Safe Practices During the Curing Process
To ensure safe practices during the curing process, it is essential to maintain a clean and organised workspace. Remove any flammable materials from the vicinity to minimise fire hazards, as ceramic coatings often require heat for curing. It is also advisable to keep a fire extinguisher within reach, in case of emergencies. Wearing appropriate personal protective equipment (PPE) such as gloves and safety goggles can protect against accidental spills or splashes of the coating material.
Monitoring the environment is crucial while the coating cures. Make sure the area is well ventilated to disperse any fumes that might be released during the process. Using fans or opening windows facilitates better airflow and reduces inhalation risks. Additionally, if the project is large or complex, consider using a temperature monitoring device to ensure that the curing temperature remains consistent and within recommended levels. This careful attention can enhance both safety and the final outcome of the ceramic coating application.
Monitoring Temperatures During Use
Temperature management is crucial when working with ceramic coatings, especially during the application and curing processes. Maintaining the right temperature ensures that the coating adheres properly and cures efficiently. It is important to use a reliable thermometer or infrared gauge to monitor the working environment. Checking temperatures regularly helps avoid any potential issues such as improper curing or damage to underlying surfaces, which could compromise the effectiveness of the coating.
In addition to using the correct instruments for temperature monitoring, implementing proper techniques can enhance safety during the application. Employing heat-resistant materials and ensuring that equipment does not overheat are essential steps. Keeping the workspace within recommended temperature limits reduces the risk of fire hazards. Awareness of the thermal properties of ceramic coatings allows for a more controlled application, promoting both safety and optimal performance.
Tools and Techniques for Safe Temperature Management
Maintaining safe temperatures during the application of ceramic coatings is crucial for both effectiveness and safety. To manage temperatures efficiently, a digital infrared thermometer can be highly beneficial. This tool allows for quick and precise temperature readings, ensuring that the surface remains within the optimal range for curing. Additionally, insulating blankets can be used to moderate temperature fluctuations, particularly in cooler environments.
Utilising heat guns can also aid in achieving the desired temperature levels without overheating the substrate. These devices offer adjustable heat settings, allowing for controlled application. Monitoring the temperature continuously with a data logger can provide real-time insights, ensuring that conditions remain safe throughout the curing process. Implementing these tools helps prevent thermal damage to the ceramic coating and the underlying surfaces.
Ventilation Requirements
Adequate airflow is crucial when working with ceramic coatings, as these materials can release volatile organic compounds (VOCs) during application and curing. Proper ventilation reduces the risk of inhaling harmful fumes and helps maintain a comfortable working environment. Employing exhaust fans and opening windows can facilitate the movement of air, ensuring that any harmful particles are dispersed quickly and do not accumulate in enclosed spaces.
In addition to passive ventilation, using air purifiers can enhance safety, particularly in confined areas. These devices can filter out particulates and VOCs, providing an extra layer of protection for users. It is also advisable to monitor air quality during the application process, allowing for timely adjustments if the concentration of harmful substances exceeds recommended levels.
Importance of Proper Airflow When Using Ceramic Coatings
Ensuring adequate airflow during the application of ceramic coatings is essential for maintaining a safe working environment. Poor ventilation can lead to the accumulation of harmful fumes and vapours that are released during the curing process. These substances can pose health risks to those in the vicinity. Proper airflow mitigates these dangers by facilitating the dispersal of these materials, reducing the likelihood of inhalation and exposure to toxic compounds.
In addition to safety concerns, effective ventilation plays a crucial role in achieving optimal results with ceramic coatings. Good airflow helps regulate temperature and humidity levels, which can directly influence the curing process. Inadequate ventilation could result in uneven curing or prolonged drying times, affecting the final finish's quality and durability. Therefore, implementing proper ventilation strategies is a vital step in the application process to ensure both safety and the integrity of the ceramic coating.
FAQS
What are ceramic coatings and why are they used?
Ceramic coatings are protective layers applied to surfaces, such as vehicles or industrial equipment, to provide durability, heat resistance, and ease of cleaning. They are often used to enhance the longevity and appearance of surfaces while offering protection against environmental damage.
How can I ensure safe curing and drying of ceramic coatings?
To ensure safe curing and drying, follow manufacturer guidelines regarding temperature and humidity levels. Always allow adequate time for the coating to cure fully and avoid exposing it to moisture or extreme temperatures during the drying process.
What temperature range should I maintain when using ceramic coatings?
It is essential to monitor temperatures according to the manufacturer's specifications, typically between 15°C and 30°C, to ensure optimal adhesion and curing of the ceramic coating.
Why is ventilation important when applying ceramic coatings?
Proper ventilation is crucial during the application of ceramic coatings to dissipate potentially harmful fumes and to ensure that the area remains safe for those working in or around it. Good airflow helps to reduce the risk of fire hazards associated with volatile organic compounds (VOCs).
What tools can I use to monitor temperatures while applying ceramic coatings?
Tools such as infrared thermometers, digital thermometers, or temperature data loggers can be used to effectively monitor and manage temperatures during the application and curing of ceramic coatings to ensure safety and optimal results.
Related Links
Best Practices for Working with High-Pressure Application ToolsEssential Safety Gear for DIY Ceramic Coating Applications
Essential Tips for Safe Mixing of Ceramic Coating Chemicals
Safety Guidelines for Handling Ceramic Coating Equipment
Importance of Skin Protection During Ceramic Coating Application
Recognising Allergic Reactions to Ceramic Coating Materials