Curing Failures: Troubleshooting Common Issues
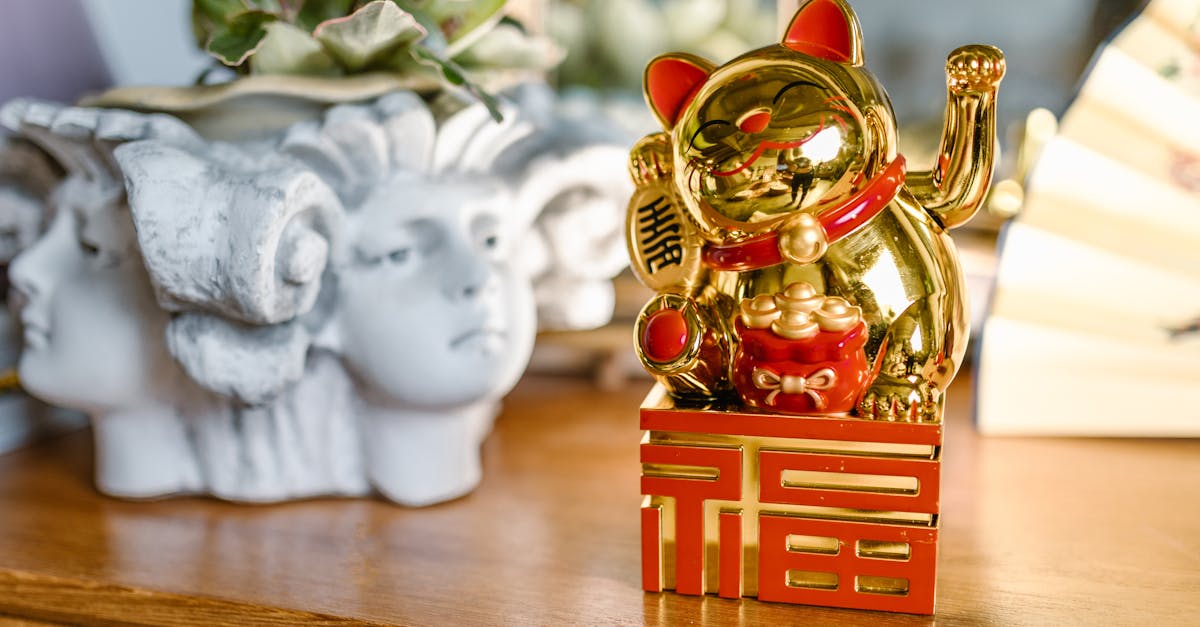
Table Of Contents
Reviewing Curing Times
Curing times are crucial to the success of any project involving adhesives or sealants. Factors such as temperature, humidity, and the specific product used can significantly influence the duration required for effective curing. Each material often has recommended curing times provided by the manufacturer, which should be adhered to for optimal results. Failing to follow these guidelines can lead to inadequate bonding or insufficient protective layers, ultimately compromising the integrity of the work.
In addition to following manufacturer recommendations, it is beneficial to regularly review curing conditions. Variations in the environment, such as changes in temperature or humidity, can affect how long a material takes to cure. It's essential to monitor these conditions throughout the curing process to ensure that they remain within acceptable levels. This attention to detail can prevent potential failures and enhance the overall performance of the product being used.
Understanding Recommended Curing Durations
Curing durations play a crucial role in achieving optimal performance for various materials. Each substance has a specific curing time that must be adhered to for the best results. Factors such as temperature, humidity and the thickness of the applied material can all impact these recommended times. Following manufacturer guidelines ensures that the curing process is efficient and effective. Deviating from these recommendations can lead to undesirable outcomes, such as incomplete curing or potential material failure.
Understanding the implications of under or over-curing is essential. Insufficient curing can lead to weak bonds, reduced durability and compromised integrity, while over-curing might cause brittleness or unwanted changes in texture. To achieve the best outcomes, regular checks should be made to verify that the conditions align with those specified in the guidelines. This attention to detail can prevent future issues and enhance the longevity and performance of the material used.
Addressing Chemical Reactions
Chemical reactions can often lead to unexpected results during the curing process. When materials show signs of not curing properly, it is essential to assess the compatibility of the components involved. Variations in formulation can result in unwanted interactions that inhibit curing. Identifying any additives or contaminants present in the mix can help pinpoint potential sources of incompatibility.
Environmental factors may also play a significant role in the curing process. Temperature and humidity fluctuations can intensify or mitigate chemical reactions. Monitoring the conditions under which the curing occurs is crucial for understanding how the environment impacts material behaviour. Adjusting these factors may improve the overall success rate of the curing process.
Identifying Incompatibility Issues
When working with diverse materials, it is crucial to assess the compatibility of the components being used. Different compounds can react adversely with one another, leading to ineffective curing or structural failures. For example, certain additives may not blend well with specific resins, resulting in separation, bubbling, or inconsistent finish. To avoid these complications, thorough research into the properties of each material is necessary before mixing or applying them.
Testing is an essential step in identifying potential compatibility issues. Small-scale trials can reveal whether particular combinations lead to undesirable reactions. By carefully evaluating the results of these tests, manufacturers can make informed decisions and adjust formulation techniques accordingly. Awareness of previous case studies and documented experiences within similar contexts can also guide troubleshooting efforts and foster greater success in curing applications.
Implementing Testing Methods
Testing methods play a critical role in assessing the success of any curing process. Several techniques can be implemented to evaluate how well materials have cured. Visual inspections offer a simple yet effective way to detect surface characteristics such as gloss and uniformity. Additionally, hardness tests can provide quantitative data, allowing for a comparison against expected standards. These methods help identify potential issues, guiding necessary adjustments in curing techniques.
More advanced methods can include tensile strength tests and thermal analysis, both of which offer deeper insights into the cured material's performance. Conducting these tests under controlled conditions ensures reliability in results. By leveraging a combination of different testing methods, practitioners can build a comprehensive understanding of curing effectiveness. This approach not only aids in correcting current processes but also enhances the overall quality of future applications.
Techniques for Evaluating Curing Success
Evaluating curing success involves a combination of visual inspections and performance tests. One effective method is to visually assess the surface for defects such as bubbles, cracks, or discolouration. Any noticeable flaws might indicate improper curing conditions or insufficient curing times. Performance tests, which can include tensile strength measurements or hardness tests, provide quantitative data on the material’s integrity and durability. These tests help determine whether the cured product meets the necessary specifications and standards.
Another approach is to conduct adhesion tests, particularly for coatings and adhesives. These tests assess how well the cured material bonds to the substrate. A simple peel test can indicate the efficacy of the curing process; if the adhesive fails to hold, it suggests that the curing was inadequate. Monitoring environmental conditions during curing, such as humidity and temperature, can also provide valuable insights into potential issues. This comprehensive evaluation ensures that any problems are addressed before moving on to further processing or application.
FAQS
What are the typical curing times for different materials?
Curing times can vary significantly depending on the material used. For example, epoxy resins may require 24 hours for initial curing, while polyurethane can take up to a week. Always refer to the manufacturer’s guidelines for specific curing times.
How can I ensure I’m using the correct curing duration?
To ensure you’re using the correct curing duration, consult the product specifications and recommended guidelines provided by the manufacturer. Environmental factors, such as temperature and humidity, can also affect curing times, so consider these conditions when planning.
What signs indicate a chemical reaction issue during curing?
Signs of a chemical reaction issue can include unusual odours, colour changes, bubbles in the material, or a sticky or tacky surface once the curing time is complete. If these symptoms are present, it may indicate an incompatibility issue or incorrect mixture ratios.
How can I identify incompatibility issues in my curing materials?
Incompatibility issues can often be identified through testing small batches before full application. If the materials do not blend well or produce unexpected results, there may be an incompatibility. Additionally, reviewing the technical datasheets for each product can provide insights into potential conflicts.
What testing methods can I implement to evaluate curing success?
To evaluate curing success, you can perform several testing methods, such as a hardness test, adhesion test, or visual inspection of the cured material. Additionally, conducting a pull-off test can help determine the bond strength and overall integrity of the cured surface.
Related Links
The Science Behind Curing: Why it Matters for Ceramic CoatingsFactors Influencing the Curing Process of Ceramic Coatings
Evaluating the Cure: Signs Your Ceramic Coating is Ready
How Environmental Conditions Affect Ceramic Coating Curing
Tips for Accelerating the Curing Time of Ceramic Coatings
Common Curing Mistakes in Ceramic Coating Application
Assessing the Curing Duration: What to Expect