Factors Influencing the Curing Process of Ceramic Coatings
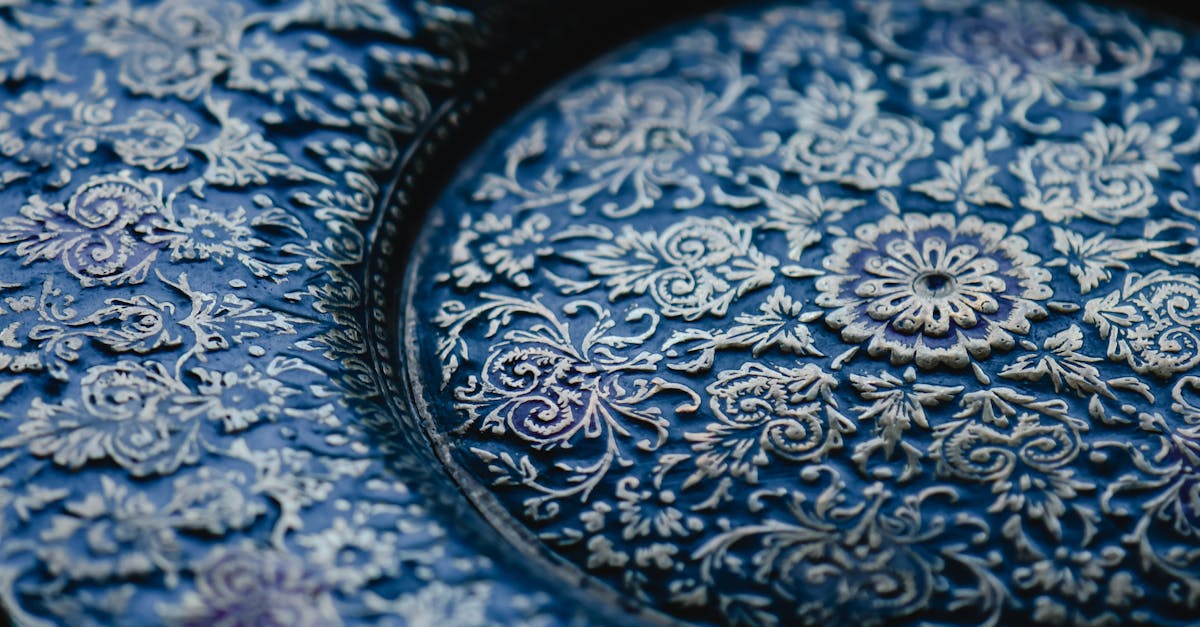
Table Of Contents
Thickness of Ceramic Coatings
The thickness of ceramic coatings plays a significant role in determining their performance and longevity. Thicker coatings can provide enhanced protection against wear, corrosion, and various environmental factors. However, increasing the thickness can also lead to challenges during the curing process. Ensuring that heat penetrates effectively through thicker layers can be difficult, which may result in uneven curing and compromised coating integrity.
Thin coatings, while easier to cure uniformly, may not offer the same level of protection as their thicker counterparts. The optimal thickness often depends on the specific application and the desired properties of the coated surface. Achieving a balance between thickness and curing efficiency is crucial to maximise the benefits of ceramic coatings while minimising potential drawbacks associated with improper curing.
How Thickness Affects Curing
The thickness of ceramic coatings plays a significant role in the curing process, impacting both adhesion and durability. Thicker coatings typically require longer curing times due to their density and the volume of material that needs to harden. Insufficient curing can lead to various issues like cracking or delamination, reducing the overall performance and lifespan of the coating.
Additionally, thicker layers may create uneven temperature gradients during the curing phase, which can affect the hardness and adhesion properties of the coating. An optimal thickness must be determined and consistently applied to ensure that the curing process is executed correctly, maximising the potential benefits of ceramic coatings in various applications.
Chemical Composition of Coatings
The chemical composition of ceramic coatings plays a fundamental role in determining their performance and durability. Different types of ceramic materials, such as alumina, zirconia, and silicon carbide, exhibit unique properties that affect thermal stability, hardness, and corrosion resistance. The specific formulation can also influence the curing process, as variations in polymer content and inorganic fillers can impact the reaction rates during the hardening phase. Understanding these elements allows manufacturers to tailor coatings for specific applications, enhancing their effectiveness in various environments.
Additives and bonding agents are crucial components within the chemical makeup of ceramic coatings. These substances can improve adhesion to substrates, enhance the coating's mechanical strength, and modify the curing characteristics to better suit the application's requirements. For instance, incorporating certain silanes can facilitate better bonding to metal surfaces, while other additives may promote more efficient crosslinking during the curing process. Careful selection and balance of these components lead to coatings that not only meet performance expectations but also exhibit longevity in demanding conditions.
Role of Additives and Bonding Agents
Additives play a pivotal role in enhancing the properties of ceramic coatings, influencing aspects such as adhesion, durability, and overall performance. Various types of additives can be integrated into the ceramic matrix, such as binders and plasticisers, which improve flexibility and help to prevent cracking during the curing process. These components facilitate better integration of the coating with the substrate, thereby enhancing the overall longevity of the coating in challenging environments.
Bonding agents also contribute significantly to the efficacy of ceramic coatings, acting as intermediaries that promote adhesion between the coating and the underlying surface. They often enhance the chemical interaction at the interface, ensuring that the coating remains securely attached over time. The choice of bonding agent can depend on the specific application and the materials involved, making it essential to tailor the formulation to achieve optimal results in terms of durability and resistance to wear.
Surface Preparation Techniques
Effective surface preparation is crucial for the success of ceramic coatings. Thorough cleaning removes contaminants such as oil, dust, and grease, which can impede adhesion. Abrasive techniques, such as sandblasting or grinding, improve the surface texture, promoting better bond strength. Ensuring a roughened surface allows the coating to mechanically interlock with the substrate, enhancing durability and longevity.
Another important aspect of surface preparation involves assessing the substrate material. Different materials may require specific treatments to achieve optimal results. For instance, metals may need a phosphating process to create a suitable surface for bonding. Understanding these variances ensures the chosen method will yield the best outcome for the particular coating system employed.
Ensuring Proper Adhesion
Proper surface preparation is a critical step in achieving optimal adhesion of ceramic coatings. This process typically involves cleaning, degreasing, and sometimes roughening the substrate to enhance the mechanical interlocking between the coating and the surface. Techniques such as sandblasting or chemical etching can effectively remove contaminants that inhibit adhesion and improve the coating's performance. Failing to adequately prepare the surface may result in delamination or flaking, compromising the coating's durability.
The choice of bonding agents also significantly influences adhesion. Additives designed to improve adhesion can be incorporated into the coating formulation or applied as a primer before the coating is applied. These agents can enhance the chemical bonding between the substrate and the ceramic layer. Additionally, they can address specific challenges posed by different substrate materials, ensuring that the coating adheres effectively regardless of the surface type. An understanding of these factors can lead to better longevity and performance of the ceramic coatings applied.
FAQS
What is the significance of the thickness of ceramic coatings in the curing process?
The thickness of ceramic coatings plays a critical role in the curing process, as it can influence the heat distribution and the time required for complete curing. Thicker coatings may take longer to cure and can lead to uneven curing if not managed properly.
How can the chemical composition of coatings affect curing?
The chemical composition of ceramic coatings determines the reaction rates during curing. Different materials can react differently to heat and environmental conditions, affecting the overall effectiveness and durability of the coating.
What role do additives and bonding agents play in the curing process of ceramic coatings?
Additives and bonding agents enhance the properties of ceramic coatings, such as adhesion and flexibility. They can also influence the curing time and the final properties of the finished coating, ensuring better performance under various conditions.
Why is surface preparation important for the curing of ceramic coatings?
Proper surface preparation is vital for achieving optimum adhesion of the ceramic coating to the substrate. Any contaminants or irregularities on the surface can hinder the curing process and affect the overall quality and durability of the coating.
What techniques can be used to ensure proper adhesion before applying ceramic coatings?
Techniques for ensuring proper adhesion include cleaning the surface to remove dust and grease, roughening the surface to increase mechanical interlock, and using primers or bonding agents designed for compatibility with the ceramic coating.
Related Links
Understanding the Ideal Curing Time for Ceramic CoatingsCuring Failures: Troubleshooting Common Issues
The Science Behind Curing: Why it Matters for Ceramic Coatings
Evaluating the Cure: Signs Your Ceramic Coating is Ready
How Environmental Conditions Affect Ceramic Coating Curing
Tips for Accelerating the Curing Time of Ceramic Coatings