Layering Strategies for Optimal Thickness in Ceramic Coating Applications
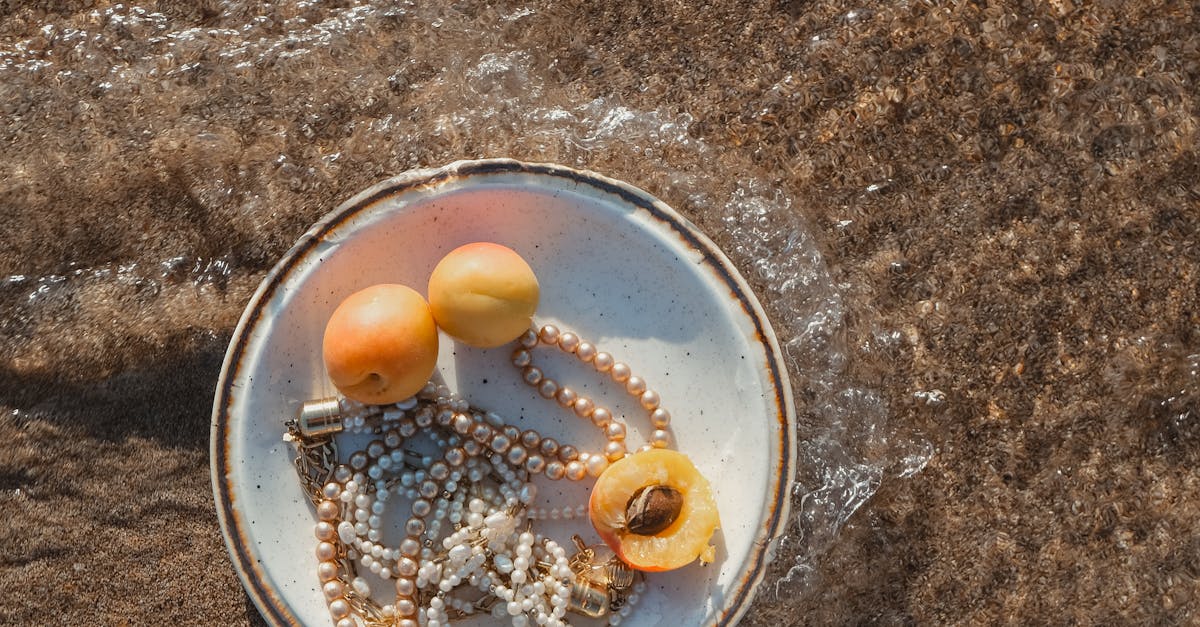
Table Of Contents
Evaluating Coating Thickness After Application
Determining the thickness of ceramic coatings after application is critical to ensuring optimal performance and durability. Various factors influence the ideal thickness, including the specific application, the environment in which the coated item will be used, and intended performance characteristics. Accurate measurement is essential, as insufficient or excessive thickness can lead to premature wear or performance failures.
Several tools and methods exist for assessing coating thickness. Non-destructive techniques, such as eddy current and ultrasonic gauges, provide quick and reliable measurements without damaging the substrate. Destructive methods may also be employed, which involve cutting or scraping the coating to examine the thickness directly. Each approach has its advantages depending on the specific requirements of the project and the materials involved.
Tools and Methods for Measuring Thickness
Accurate measurement of coating thickness is essential to ensure optimal performance and longevity. Several tools are available for this purpose, including ultrasonic thickness gauges, which utilise sound waves to determine material thickness, and magnetic induction gauges, designed for ferrous substrates. Each tool offers unique advantages; ultrasonic gauges can assess coatings on any substrate without damaging the surface, while magnetic induction tools provide rapid readings for ferrous materials.
Digital micrometers represent another approach, offering precise thickness readings by directly contacting the surface. These instruments are particularly valuable for small-scale applications where high accuracy is paramount. Additionally, X-ray fluorescence (XRF) can be employed for non-destructive testing, especially in complex or layered coatings. Employing the appropriate method for measuring thickness ensures that the coating adheres to specified tolerances, ultimately enhancing the reliability of ceramic applications in various scenarios.
The Role of Curing in Layering Strategies
Curing plays a critical role in determining the effectiveness and durability of ceramic coatings. The process involves maintaining optimal environmental conditions to allow the coating to chemically and physically bond to the substrate. Insufficient curing can lead to issues such as inadequate adhesion, compromised thickness, and ultimately deteriorated performance. Ensuring that the coating receives the right amount of time and temperature for curing promotes the desired properties, such as hardness and resistance to wear.
Different curing methods can influence the outcome of ceramic layering strategies. For instance, heat curing accelerates the hardening process, while air curing relies on environmental factors. Understanding the specific requirements of each ceramic formulation is essential for achieving the intended results. Adapting curing techniques to suit the application method and product characteristics ensures enhanced efficiency and longevity of the coating.
Best Practices for Proper Curing Techniques
Maintaining the right environmental conditions during the curing process is crucial for achieving optimal results. Temperature and humidity levels should be controlled to ensure that the coatings cure effectively without developing defects. Excessive humidity can lead to improper adhesion, while low temperatures may slow down the curing rate. Attention should also be given to the surface preparation prior to application, as a clean and dry substrate will improve the coating’s performance.
Monitoring the curing time is equally important, as this can affect the durability and final appearance of the ceramic coating. Different formulations may have varying curing requirements, so it's essential to follow the manufacturer's specifications closely. Implementing periodic inspections during the curing phase can help identify any issues early on. This proactive approach allows for adjustments and potentially prevents costly mistakes, ensuring the integrity and longevity of the ceramic layer.
Case Studies in Layering Success
Different industries have successfully implemented layering strategies to enhance the performance of ceramic coatings. In the automotive sector, a leading manufacturer utilised a multi-layered ceramic coating on its vehicles to increase resistance to scratches and corrosion. The application involved layering a base coat, followed by a mid-coat and a topcoat, resulting in substantial improvements in aesthetic appeal and durability. Testing revealed that the coatings could withstand harsh environmental conditions, ensuring long-lasting protection for the vehicles.
Similarly, the aerospace industry has employed strategic layering techniques to protect components subject to extreme temperatures and wear. A notable example involved the application of a thermal barrier coating on jet engine parts. The engineers layered multiple ceramic compositions, optimising thermal resistance and reducing heat transfer effectively. This approach not only extended the lifespan of engine components but also improved overall efficiency, demonstrating the significant benefits of tailored layering strategies in high-performance applications.
Examples of Effective Layering in Various Industries
In the automotive industry, ceramic coatings have gained significant traction due to their ability to enhance durability and aesthetics. Manufacturers often apply multilayer coatings to achieve optimal thickness, ensuring that the exterior finishes are not only visually appealing but also resistant to environmental damage. For example, a luxury car maker recently implemented a three-layer ceramic coating system, including a base layer for adhesion, a middle layer for protection, and a final clear layer for gloss. This approach resulted in a finish that stood up to harsh conditions while maintaining an impressive shine.
Similarly, the aerospace sector has recognised the value of layering strategies with ceramic coatings. Aircraft components are subjected to extreme temperatures and corrosive elements, necessitating coatings that can withstand these rigorous demands. A notable case involved a commercial airline that adopted a two-layer ceramic coating system for its engine components. The first layer provided thermal resistance, while the second cut down on friction, leading to improved fuel efficiency and reduced wear over time. Such applications illustrate how effective layering can significantly enhance performance and longevity across diverse industries.
FAQS
What is the importance of coating thickness in ceramic coating applications?
Coating thickness is crucial in ceramic coating applications as it directly affects durability, protection, and performance. An optimal thickness ensures the coating can withstand environmental factors and provides the desired aesthetic appeal.
How can I measure the thickness of a ceramic coating after application?
Thickness can be measured using various tools such as micrometers, ultrasonic thickness gauges, or magnetic induction gauges, depending on the substrate and coating type. Each method has its advantages and can provide accurate readings.
What role does curing play in achieving optimal layering strategies?
Curing is essential as it allows the coating to develop its full hardness and adhesion properties. Proper curing ensures that the layers bond effectively, reducing the risk of delamination and enhancing overall performance.
What are some best practices for curing ceramic coatings?
Best practices for curing include following the manufacturer's guidelines regarding temperature and humidity, ensuring adequate ventilation, and allowing sufficient time for each layer to cure before applying the next. Monitoring these factors can greatly enhance the coating's effectiveness.
Can you provide examples of successful layering strategies in different industries?
Yes, successful layering strategies can be observed in industries such as automotive, aerospace, and industrial manufacturing. For instance, in the automotive sector, layered ceramic coatings are used to enhance paint durability and resistance to scratches, while in aerospace, layered coatings improve thermal resistance and reduce weight.
Related Links
Spray vs. Wipe Application: Choosing the Right Method for Ceramic CoatingThe Role of Temperature and Humidity in Ceramic Coating Application
Strategies for Applying Ceramic Coating on Curved and Complex Shapes
Timing Techniques: When to Reapply and Layer Ceramic Coatings
Overhead Application Techniques for Hard-to-Reach Areas in Coating