The Role of Temperature and Humidity in Ceramic Coating Application
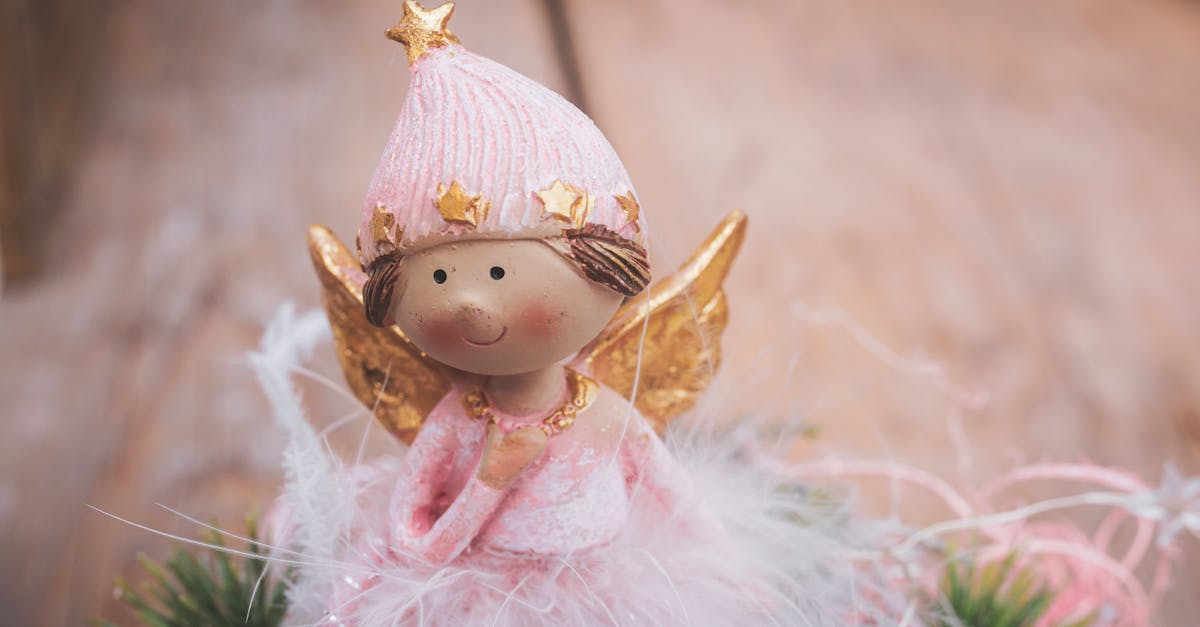
Table Of Contents
Application Techniques
The application of ceramic coatings requires precision to ensure successful adhesion and durability. Techniques such as spray application, dip coating, and brush application tend to be used depending on the complexity and scale of the project. Spray application is often favoured for its ability to create a uniform layer, minimising the risk of imperfections that may arise when using other methods. By adjusting the nozzle size and distance from the surface, operators can achieve optimal coverage and thickness vital for performance.
Proper surface preparation is crucial for achieving strong adhesion. Cleaning and priming the substrate can significantly influence the coating's effectiveness. Additionally, operators should be aware of the importance of maintaining a consistent coating temperature throughout the application process. Fluctuations can affect the viscosity of the material, leading to variable application results. By being mindful of these factors, users can enhance the overall effectiveness of the ceramic coating.
Adjusting Techniques Based on Environmental Conditions
When applying ceramic coatings, environmental conditions such as temperature and humidity significantly influence the techniques used. For higher temperatures, it is advisable to adjust the spray technique, moving at a faster pace to prevent overheating the coating layer. The faster application reduces the risk of defects like sagging or running, ensuring an even finish without excessive material buildup.
In contrast, increased humidity can lead to issues such as extended curing times and potential moisture entrapment within the coating. Lowering the spray pressure during application may help mitigate these effects, allowing a finer mist to form that adheres better to the surface. This technique encourages the coating to settle properly, minimizing the risk of blooming or haziness that often arises in humid conditions.
Curing Process Variables
The curing process for ceramic coatings is influenced significantly by environmental variables such as temperature and humidity. High temperatures can accelerate curing times, leading to a faster hardening of the coating. However, if temperatures exceed recommended limits, it can cause issues like bubbling or peeling. Conversely, low temperatures may extend curing periods, which risks trapping moisture within the coating, creating imperfections.
Humidity levels also play a crucial role in the curing process. Higher humidity can lead to slower evaporation of solvents, causing a tacky surface that may not cure properly. Additionally, humidity can introduce water into the coating mixture, which can adversely affect adhesion and durability. A careful balance is necessary to optimise the curing environment, ensuring that the final finish is both aesthetically pleasing and functionally robust.
Temperature and Humidity During Curing
The curing phase of ceramic coatings is significantly influenced by temperature and humidity levels. High temperatures can accelerate the curing process, potentially leading to issues like shrinkage or cracking if the material cures too quickly. Conversely, low temperatures may prolong the curing time, resulting in a weaker bond if the coating does not achieve its optimal hardness within the recommended period. Thus, it is critical to monitor the curing environment and adjust application techniques accordingly.
Humidity also plays a vital role during the curing phase. Elevated humidity levels can lead to moisture retention that interferes with the curing process, thereby affecting the final hardness and adhesion of the coating. It is essential to maintain a balance; an ideal relative humidity level helps ensure that the ceramic coating cures properly and achieves the desired properties. Modifying curing techniques based on both temperature and humidity can help mitigate these risks and promote a successful application.
Troubleshooting Common Issues
When applying ceramic coatings, various environmental factors can lead to unexpected challenges. Issues such as improper adhesion, uneven texture, or discolouration often stem from temperature and humidity levels during application. If the ambient conditions are too humid, excess moisture can interfere with the bonding process. Similarly, high temperatures can cause coatings to dry too quickly, preventing proper adhesion.
Identifying problems effectively requires careful observation of the application environment. Noticing any bubbling or peeling indicates that humidity may have been too high during the process. Discolouration or a rough finish might suggest that the coating dried too rapidly in overly warm conditions. By remaining vigilant and adjusting techniques accordingly, operators can mitigate these common complications and ensure a successful coating application.
Identifying Problems Related to Environmental Factors
Environmental factors can significantly influence the outcome of ceramic coating applications. High humidity levels often lead to issues such as improper bonding and surface imperfections. Moisture in the air can affect the drying time, resulting in an uneven finish. Similarly, extreme temperature variations can cause problems like cracking or inadequate curing, which may compromise the integrity of the coating.
Moreover, ignoring these environmental conditions can lead to lasting implications for the coating's performance. For instance, applying the coating in cold settings may slow down the chemical reactions essential for curing. On the other hand, excessive heat can expedite the process, potentially trapping solvent gases. Both scenarios can ultimately impede the durability and appearance of the ceramic coating, requiring careful attention and adjustment during application.
FAQS
Why is temperature important in ceramic coating application?
Temperature affects the viscosity of the ceramic coating, the adhesion to the substrate, and the curing process, making it essential for achieving a durable and effective finish.
How does humidity influence the curing process of ceramic coatings?
High humidity can slow down the curing process, leading to improper adhesion and potential issues like bubbling or peeling. Low humidity, on the other hand, can cause the coating to dry too quickly, resulting in cracks.
What is the ideal temperature range for applying ceramic coatings?
The ideal temperature range for applying ceramic coatings is typically between 15°C to 30°C. However, it is important to refer to specific product guidelines as formulations can vary.
Can I apply ceramic coatings in extreme weather conditions?
It is generally not recommended to apply ceramic coatings in extreme weather conditions, such as very high or low temperatures and high humidity. Such conditions can negatively impact the application and curing processes.
What should I do if I encounter issues with my ceramic coating related to temperature or humidity?
If you experience issues with your ceramic coating, such as uneven application or poor adhesion, assess the environmental conditions during application and curing. You may need to adjust your techniques or wait for more suitable conditions before reapplying.
Related Links
Layering Strategies for Optimal Thickness in Ceramic Coating ApplicationsTechniques for Achieving an Even Application of Ceramic Coating
Strategies for Applying Ceramic Coating on Curved and Complex Shapes
Timing Techniques: When to Reapply and Layer Ceramic Coatings
Overhead Application Techniques for Hard-to-Reach Areas in Coating