Understanding the Ideal Curing Time for Ceramic Coatings
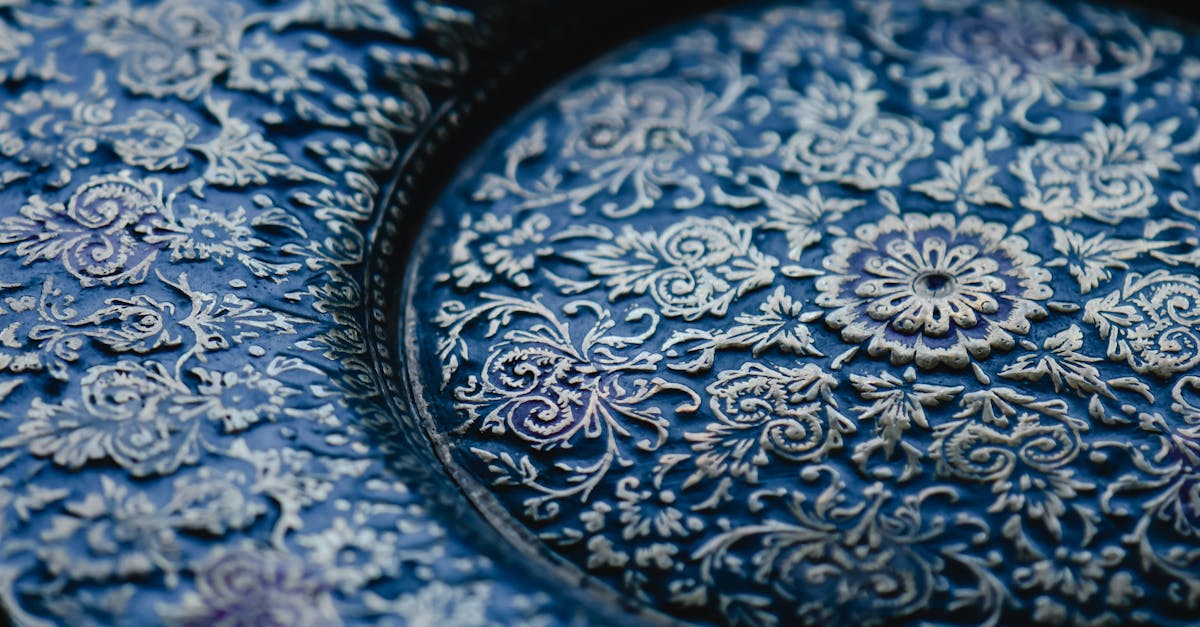
Table Of Contents
How to Test if a Ceramic Coating is Fully Cured
Determining whether a ceramic coating has fully cured involves both visual and physical assessments. A well-cured coating typically exhibits a smooth, glossy surface without any imperfections. Inspect for any signs of haziness or wet spots, as these can indicate incomplete curing. Additionally, a simple water bead test can be performed—if water beads up neatly on the surface, it suggests that the coating has reached its optimal state of curing.
Physical indicators also play a key role in assessing the curing process. Touch the surface gently; it should feel firm and dry rather than tacky or soft. Additionally, check for resistance against scratches or abrasions. A fully cured coating should withstand minimal damage during light contact. Testing these aspects will ensure that the ceramic coating is not only visually appealing but also provides the protective benefits intended.
Visual and Physical Indicators
Observing surface sheen can provide insights into the curing status of a ceramic coating. A fully cured coating typically exhibits a deep, glossy finish that reflects light uniformly. In contrast, a coating that has not yet cured completely may show cloudy or dull areas, indicating that the chemical reaction is still ongoing. Additionally, checking for any soft or tacky spots can reveal whether the coating has set adequately. Areas that feel sticky or less rigid suggest that more time is needed for optimal curing.
Physical touch can also yield helpful information about the cure state; a properly cured ceramic coating should feel smooth and solid to the touch. Scanning for imperfections, like swirl marks or uneven textures, might indicate that the application was flawed or that the curing process has not reached its desired stage. Using a gentle pressure test can further help assess the hardness of the surface. If it yields easily, further curing time is essential for achieving the maximum durability and effectiveness of the ceramic coating.
Tips for Ensuring Optimal Curing
To achieve the best results with ceramic coatings, surface preparation is crucial. Start by thoroughly cleaning the area to remove any dirt, grease, or residues. Use a suitable degreaser to ensure that the surface is free from contaminants. After cleaning, it’s essential to dry the surface completely before application. Any moisture can interfere with the bonding process of the coating, ultimately affecting its performance. Ensuring a smooth and clean surface allows the coating to adhere properly, leading to optimal protection.
It is also vital to apply the ceramic coating under recommended environmental conditions. Ideal temperature and humidity levels can significantly impact curing times and overall effectiveness. Avoid applying coatings during extreme weather, such as very high humidity or intense sunlight. Working in a shaded area can provide a more controlled environment, which is beneficial for achieving even application and curing. Regularly checking the manufacturer’s instructions will provide guidance on the ideal conditions for specific products. Following these tips will enhance the longevity and protective qualities of the ceramic coating.
Preparing the Surface Before Application
Thorough preparation of the surface is essential to ensure optimal adhesion of ceramic coatings. Begin by washing the area meticulously to remove any dirt, grime, or old wax residues that could interfere with the bonding process. It's advisable to use a pH-neutral car shampoo for best results. After washing, drying the surface with a microfibre towel prevents water spots and ensures no moisture is present, which could compromise the coating.
Next, inspecting the paint condition is crucial. Any imperfections such as scratches or swirl marks should be addressed prior to application. Polishing the surface not only improves the finish but also helps the ceramic coating adhere better. Once the surface is clean, dry, and free of defects, it is ready for the application of the ceramic coating, setting the stage for optimal performance and durability.
Curing Times for Various Types of Ceramic Coatings
Different ceramic coatings exhibit varying curing times, largely influenced by their chemical formulations and intended applications. Typically, consumer-grade ceramic coatings can take anywhere from 24 to 48 hours to cure adequately under average environmental conditions. More advanced or professional-grade products often require longer periods, sometimes extending to a week for full hardness and resistance to environmental factors. These differences can affect the timing of subsequent applications or the use of the coated item.
Environmental conditions play a significant role in the curing process. Factors such as humidity, temperature, and airflow can either accelerate or hinder the curing of ceramic coatings. A warmer environment tends to promote faster curing times, while high humidity can lead to extended periods before a coating reaches full hardness. Understanding these variables is crucial when choosing a ceramic coating and planning its application to achieve optimal results.
Comparing Different Products
When exploring the variety of ceramic coatings available on the market, it is essential to consider their specific curing times and application techniques. Some products boast rapid curing, allowing for quicker use after application, while others may require a longer period to achieve their optimal hardness and durability. Differences in formulations can significantly impact not only the curing speed but also the overall performance of the coating.
Comparison of ceramic coatings should also take into account factors such as durability, chemical resistance, and ease of application. Brands often vary in the quality of ingredients they use, which can affect both the appearance and longevity of the finished surface. Thorough research and user reviews can provide valuable insights, helping to identify which products deliver the best results based on individual needs and conditions.
FAQS
What is the ideal curing time for ceramic coatings?
The ideal curing time for ceramic coatings can vary depending on the specific product, but it typically ranges from 24 hours to several days for full curing. Always refer to the manufacturer's guidelines for the best results.
How can I test if a ceramic coating is fully cured?
To test if a ceramic coating is fully cured, you can look for visual and physical indicators such as a hard, glossy finish, and perform a light scratch test in an inconspicuous area. If the coating remains intact without any damage, it is likely fully cured.
What factors can affect the curing time of ceramic coatings?
Factors that can affect the curing time include temperature, humidity, and the thickness of the applied layer. Higher temperatures and lower humidity levels generally accelerate curing, while vice versa can prolong it.
Is it necessary to wait for the full curing time before washing the vehicle?
Yes, it is advisable to wait for the full curing time before washing the vehicle to ensure the coating has properly set and bonded to the surface, which maximises its protective qualities.
Can I speed up the curing process of ceramic coatings?
While you cannot drastically speed up the curing process, you can ensure optimal conditions by applying the coating in a warm, dry environment and avoiding excessive moisture or cold temperatures during the curing phase.
Related Links
Optimal Temperature and Humidity Conditions for CuringFactors Influencing the Curing Process of Ceramic Coatings
Curing Failures: Troubleshooting Common Issues
The Science Behind Curing: Why it Matters for Ceramic Coatings
Evaluating the Cure: Signs Your Ceramic Coating is Ready