Proper Ventilation Techniques for Ceramic Coating Spaces
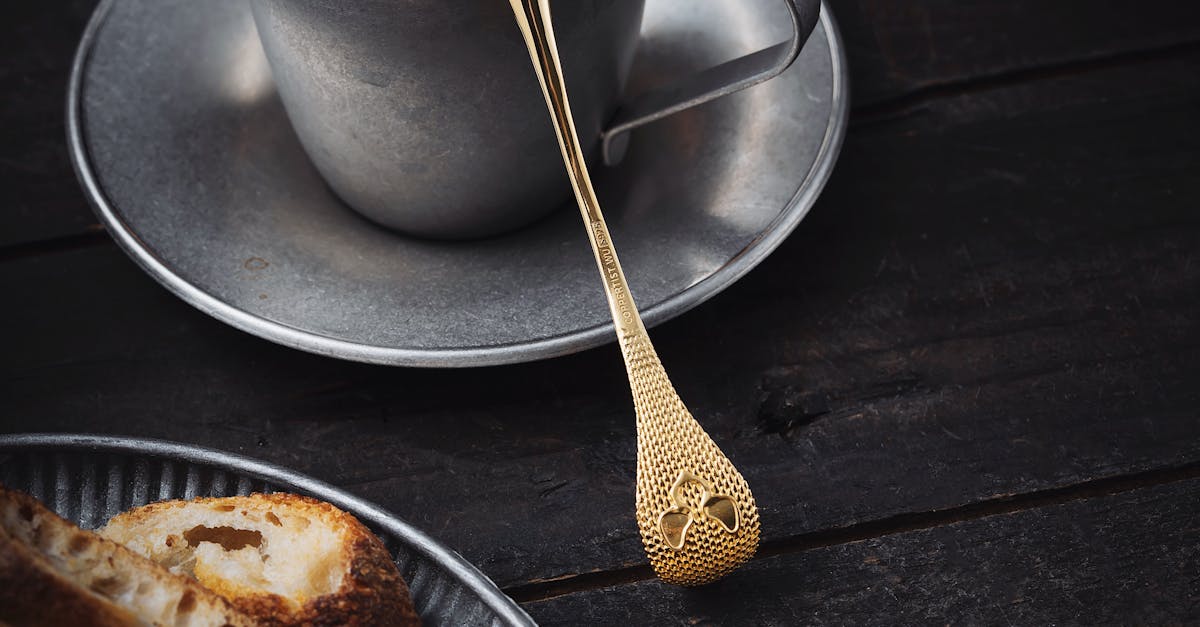
Table Of Contents
Safety Protocols for Ventilation
Ensuring the safety of personnel during ceramic coating applications is crucial. Proper ventilation helps mitigate the risks associated with harmful fumes and particulate matter. Regular monitoring of air quality within the workspace is essential. This can be achieved through the use of air quality sensors, which detect the concentration of volatile organic compounds (VOCs) and other hazardous substances. Establishing a routine for checking ventilation systems is necessary. Clean filters and well-maintained exhaust systems can significantly improve airflow and reduce exposure to contaminants.
Integrating safety protocols into daily operations enhances overall workplace health. Signage indicating areas requiring ventilation and personal protective equipment (PPE) use fosters a culture of safety. Training employees on best practices for using ventilation equipment is vital. Workers should understand how to navigate potential hazards associated with ceramic coating processes. Ensuring easy access to PPE, such as respirators and masks, further reinforces safety measures. Involving all staff in discussions about ventilation strategies can lead to better implementation and adherence to safety protocols.
Protective Gear and Best Practices
Ensuring the safety of all personnel involved in the ceramic coating process is critical. Wearing appropriate protective gear significantly reduces exposure to harmful fumes and particulate matter. Essential items include respirators or masks equipped with the correct filters to safeguard against inhalation of volatile organic compounds. Additionally, gloves resistant to chemicals protect hands from direct contact with materials, while safety goggles should be worn to shield eyes from splashes and irritants.
Alongside proper gear, adopting best practices enhances overall safety during coating applications. Regular training sessions on the proper use of equipment encourage adherence to safety standards. Implementing a buddy system ensures that at least one person monitors conditions, contributing to a safer working environment. Keeping the workspace tidy reduces the risk of accidents and allows for better airflow, which is essential for maintaining an effective ventilation system.
Designing an Efficient Ventilation Layout
Creating an efficient ventilation layout requires careful consideration of the space's dimensions and usage patterns. Positioning exhaust fans and intake vents strategically enhances airflow, which is crucial during the ceramic coating process. Ventilation should be designed to facilitate the removal of harmful fumes and particulates generated by the coatings, ensuring that fresh air is drawn in from outside. It is essential to account for the natural flow of air within the facility. This can involve studying airflow patterns and avoiding obstructions that could hinder circulation.
Incorporating adjustable vents and ducts can offer flexibility to the ventilation system. This adaptability allows operators to modify airflow based on specific tasks or conditions. A combination of ceiling-mounted and wall-mounted units often provides a balanced air distribution throughout the space. Regular assessments of the layout can help identify areas that may benefit from additional ventilation or modification. Avoiding a one-size-fits-all approach is vital; customising the layout to suit the unique requirements of the environment promotes safer and more efficient working conditions.
Key Elements of Space Design
Properly designed spaces enhance the effectiveness of ventilation systems in ceramic coating environments. Consider the layout of machinery and equipment; sufficient distance between items allows for optimal airflow. Positioning air intake and exhaust vents strategically can prevent stagnant zones where fumes and particulate matter may accumulate. Natural light and adequate space for movement further contribute to an improved work environment.
Another essential aspect is material choice for walls and surfaces. Non-porous materials are preferable as they do not absorb contaminants and are easier to clean. Installing barriers or partitions can define work areas and guide airflow more efficiently. Ensuring that vents are unobstructed and regularly maintained is critical for sustaining a well-ventilated atmosphere that prioritises worker safety and product quality.
Common Ventilation Mistakes to Avoid
One common mistake in ventilation design is neglecting the proper placement of exhaust fans. These fans should be installed in areas where contamination is likely to accumulate. When positioned incorrectly, they can fail to effectively remove harmful fumes, resulting in poor air quality within the workspace. Additionally, using fans that are not powerful enough for the size of the room can exacerbate the issue, leading to potential health risks for those conducting ceramic coating work.
Another frequent oversight is overlooking the importance of fresh air intake. Many spaces rely solely on exhaust systems, which can create negative pressure if not balanced with an adequate supply of fresh air. This imbalance may lead to airflow stagnation and an unhealthy environment. It's essential to ensure that intake vents are unobstructed and strategically placed to allow for sufficient airflow exchange throughout the area.
Identifying Airflow Blockages
Effective airflow is crucial for maintaining a safe and productive workspace, particularly in areas where ceramic coating takes place. Blockages can significantly hinder the effectiveness of ventilation systems. Identifying these obstructions early can prevent the accumulation of harmful fumes and maintain a more stable environment. Common signs include stagnant air, uneven temperatures, or persistent odours that linger in the space.
Regular inspections are essential for detecting airflow issues. Inspect ductwork and vents for signs of dirt buildup or physical obstructions. Ensure that fans and exhaust systems operate efficiently without any hindrances. It is also vital to monitor for furniture or equipment placement that could interfere with airflow pathways. By proactively addressing these concerns, you can enhance the overall efficiency of the ventilation system and ensure a healthier workspace.
FAQS
Why is proper ventilation important in ceramic coating spaces?
Proper ventilation is crucial in ceramic coating spaces to ensure the safe dispersal of fumes and particulate matter, minimise the risk of respiratory issues, and maintain a comfortable working environment.
What type of protective gear should be worn when working in a ceramic coating space?
It is recommended to wear respiratory masks, gloves, goggles, and protective clothing to safeguard against harmful chemicals and dust particles during the coating process.
What are some key elements to consider when designing a ventilation layout for ceramic coating spaces?
Key elements include the placement of exhaust fans, the use of filtered air intakes, ensuring adequate airflow paths, and avoiding obstructions that could impede the movement of air.
What are common ventilation mistakes to avoid in ceramic coating areas?
Common mistakes include insufficient airflow, neglecting to install filtration systems, obstructing air pathways with equipment or materials, and failing to regularly maintain ventilation systems.
How can I identify airflow blockages in my ceramic coating workspace?
To identify airflow blockages, check for visible obstructions around vents and exhaust systems, listen for unusual sounds from fans, and use smoke tests or anemometers to assess airflow patterns and flow rates.
Related Links
First Aid Measures for Ceramic Coating AccidentsUnderstanding Chemical Hazards in Ceramic Coating Products
Fire Safety Measures When Using Ceramic Coatings
Best Practices for Working with High-Pressure Application Tools
Essential Tips for Safe Mixing of Ceramic Coating Chemicals
Safety Guidelines for Handling Ceramic Coating Equipment
Importance of Skin Protection During Ceramic Coating Application